END USER: Sigma Machine Inc., (269) 345-6316, www.sigmamachine.net.
CHALLENGE: Eliminate excess coolant to improve shop floor safety and cleanliness.
SOLUTION: Minimum quantity lubrication systems.
SOLUTION PROVIDER: Unist Inc., (800) 253-5462, www.unist.com.
Around 2 years ago, Sigma Machine Inc. was a mess. Literally, coolant covered the floors of the Kalamazoo, Mich., aluminum-extrusion machine shop, operators tracked it from the shop floor to the offices, and the slippery fluids posed a safety hazard. Also, the shop’s floors are epoxy painted and the work area is brightly lit, which only made the watery mess more noticeable.
To combat this issue, the shop installed minimum quantity lubrication (MQL) systems from Unist Inc., Grand Rapids, Mich., on its CNC mills—but the result was more than a clean floor.
“The original issue was simple housekeeping,” said Jim Van Weelden, president and owner of Sigma Machine, “but once we made the switch, there were a number of benefits that we got that we weren’t even looking for in the first place. Our maintenance costs are way down because there are fewer coolant tanks to be purged and less coolant to be disposed of, and our cycle times have decreased because we’re able to run the machines at higher speeds.”
The newly clean work environment is important not only to management, but to the 100 employees who work there. While coolant was being tracked all over the building and, presumably, back to employees’ cars and homes, employees can now come to work clean and go home clean.
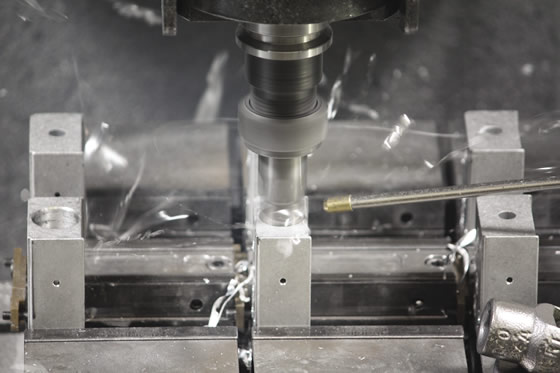
A Unist MQL system is used in a milling operation.
Sigma Machine outfitted about 30 CNC mills on the main shop floor with the standard Unist 2210 MQL system, and Van Weelden said the shop plans to upgrade to the newest Unist MQL system later this year, which will offer several benefits. “Our next project is to go through-spindle and through-tool with Unist, which is offered with their new programmable system,” he said. “We are just starting to get the components together to test it on one machine. If that goes well, we will refit most of our machines with that system.”
Retrofitting a CNC mill with a standard Unist MQL system costs about $2,500, while the new through-tool, programmable system costs about $4,500 per machine. Two years after installing the standard systems, Sigma is realizing a return on investment from reduced maintenance costs, according to Van Weelden.
The only challenge Sigma ran into when incorporating MQL was correctly training machinists who are accustomed to working with flood coolant. “Operators who are used to standard water-based coolant tend to clear chips with the MQL-laden air from the machine,” Van Weelden noted. This created a fog which was bothering some workers’ throats.
Unist Senior Vice President Tim Walker added, “Although commonly caused a ‘mist system,’ MQL systems have been shown to produce fewer emissions than flood cooling when adjusted properly.” Getting machinists to adjust to the MQL mentality isn’t always easy, he continued, as the natural tendency is to think that if a little lubricant is good, more must be better. The excess lubricant has no place to go and winds up in the air. “We find that once our customers find the lubrication ‘sweet spot’ with their MQL systems, they quickly fall in love with the benefits.”
“We had a very simple, very narrow goal in mind initially,” Van Weelden said, “but the benefits have been much more than just cleanliness. This last year, we purchased 12 new mills, and, based on the results from our first year of operation, we ordered 12 new Unist systems at the same time. There’s just no reason we’d use anything else.”
Related Glossary Terms
- computer numerical control ( CNC)
computer numerical control ( CNC)
Microprocessor-based controller dedicated to a machine tool that permits the creation or modification of parts. Programmed numerical control activates the machine’s servos and spindle drives and controls the various machining operations. See DNC, direct numerical control; NC, numerical control.
- coolant
coolant
Fluid that reduces temperature buildup at the tool/workpiece interface during machining. Normally takes the form of a liquid such as soluble or chemical mixtures (semisynthetic, synthetic) but can be pressurized air or other gas. Because of water’s ability to absorb great quantities of heat, it is widely used as a coolant and vehicle for various cutting compounds, with the water-to-compound ratio varying with the machining task. See cutting fluid; semisynthetic cutting fluid; soluble-oil cutting fluid; synthetic cutting fluid.
- gang cutting ( milling)
gang cutting ( milling)
Machining with several cutters mounted on a single arbor, generally for simultaneous cutting.
- milling
milling
Machining operation in which metal or other material is removed by applying power to a rotating cutter. In vertical milling, the cutting tool is mounted vertically on the spindle. In horizontal milling, the cutting tool is mounted horizontally, either directly on the spindle or on an arbor. Horizontal milling is further broken down into conventional milling, where the cutter rotates opposite the direction of feed, or “up” into the workpiece; and climb milling, where the cutter rotates in the direction of feed, or “down” into the workpiece. Milling operations include plane or surface milling, endmilling, facemilling, angle milling, form milling and profiling.
- milling machine ( mill)
milling machine ( mill)
Runs endmills and arbor-mounted milling cutters. Features include a head with a spindle that drives the cutters; a column, knee and table that provide motion in the three Cartesian axes; and a base that supports the components and houses the cutting-fluid pump and reservoir. The work is mounted on the table and fed into the rotating cutter or endmill to accomplish the milling steps; vertical milling machines also feed endmills into the work by means of a spindle-mounted quill. Models range from small manual machines to big bed-type and duplex mills. All take one of three basic forms: vertical, horizontal or convertible horizontal/vertical. Vertical machines may be knee-type (the table is mounted on a knee that can be elevated) or bed-type (the table is securely supported and only moves horizontally). In general, horizontal machines are bigger and more powerful, while vertical machines are lighter but more versatile and easier to set up and operate.