Flame straightening is one of those old-timer skills everybody has heard of but few have had the opportunity to witness. The ability to straighten bent plates and shafts is almost magical in its simplicity. It’s definitely a valuable skill if you intend to spend any time around a welding shop, unless you relish the thought of beating a stubborn shaft or plate into submission with a mallet. This technique has been used to straighten everything from the hulls of ships to samurai swords.
Metalworkers are continually confronted with the negative aspects of joining metals by welding. Whenever metal is heated, it expands and not always in a favorable way. Most often it has a negative impact on the end product. The results are manifested as warpage, distortion and stress. If you have spent any time in a welding shop, you have seen some of these types of distortion, like welds pulling, flame-cut strips and shapes twisting and bowing, and oil-canned plates.
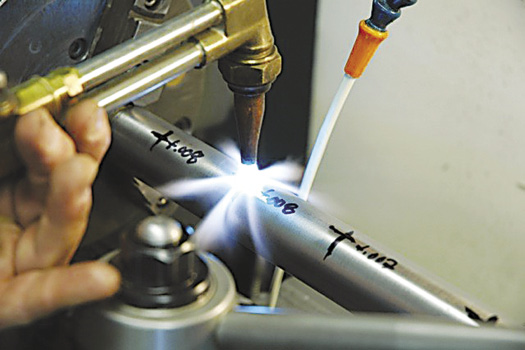
Flame straightening is an easy-to-learn technique for correcting bent plates and shafts.
Every welded structure will try to seek the position of least-stored stress. A good illustration is when you tightly crumple up a sheet of paper and drop it on a desk. The paper expands slightly and finally settles in the position of least-internal stress. When welding on a metal structure, this is happening continuously. The weldment is undergoing a constant rearrangement to find this state of least stress.
Welding sequence, clamping and fixturing can help, but can never eliminate the effects of expanding hot metal. When you stress-relieve a weldment or part, you are allowing remaining locked-in stress to dissipate via heating or vibration.
Flame straightening uses the same principles that cause warpage or distortion to make positive corrections. The best way to imagine how this process works is something like reverse welding. An example is using the effects of controlled distortion to induce a large camber. These kinds of results can be accomplished with the humble cutting torch and the knowledge of where to apply the technique.
So what is flame straightening exactly? I define it as the specific application of controlled cycles of heating and cooling that are used to correct, enhance or minimize distortion in metals.
Flame straightening causes a contraction or localized shrinking in metals used to effect changes in geometry. The technique is applied with a common oxy-acetylene torch in a specific way that induces the maximum amount of contraction.
Now, before you run out to the shop and fire up your torch, there are a few important points you should know. Flame straightening works best when the distortion is caused by welding or is related to heat. It can be used on any material that has no restrictions on the application of heat from an oxy-acetylene torch. It works best with materials that do not have high thermal conductivity. Steel and stainless steel are the primary candidates, while aluminum and copper are less than enthusiastic about this technique.
A typical weld distortion problem involves two fillet welds joining two tubes that have bowed the long tube. Some of this bowing could be eliminated by good fixturing and clamping, but effective flame straightening will correct the problem.
Unlike pressure methods, such as hydraulic presses and screw jacks, flame straightening is the laser-guided smart bomb that attacks the exact offending areas. Pressure methods distribute their gross application of forces throughout the structure and sometimes cause more harm than good. Hydraulic rams further complicate the correcting measures because they lack a sense of feel connected with the yield point of a particular material. Unless you have a good pressure gage to monitor force application, the yield point can be a dangerous, easily-exceeded target.
Pressure methods require the parts to be supported so the force can be applied. Flame straightening is suitable where pressure methods would be impossible or extremely awkward. CTE
Related Glossary Terms
- fillet
fillet
Rounded corner or arc that blends together two intersecting curves or lines. In three dimensions, a fillet surface is a transition surface that blends together two surfaces.
- yield point
yield point
First stress in a material, usually less than the maximum attainable stress, at which an increase in strain occurs without an increase in stress. Only certain metals exhibit a yield point. If there is a decrease in stress after yielding, a distinction may be made between upper and lower yield points.