END USER: Potomac Photonics Inc., (888) 919-1303, www.potomac-laser.com.
CHALLENGE: Increase part quality and productivity when deep-cavity micromachining while achieving tight tolerances.
SOLUTION: A heat-activated, wax-based compound for holding parts.
SOLUTION PROVIDER: Mitee-Bite Products LLC, (800) 543-3580, www.miteebite.com.
Potomac Photonics Inc. is no stranger to small stuff. The Baltimore-based company has provided micromachining services to the medical, electronic, aerospace and automotive industries, among others, since 1982. However, a polymeric part about 0.5 mm (0.02 ") in diameter and 5mm (0.19 ") deep presented unique challenges. The part needed to be machined from both sides, necessitating a strong, but low-temperature and easily removable workholder that would allow the company to maintain the specified diameter tolerances of ±5µm (0.0002 ").
According to Amir Harandi, Ph.D., senior R&D engineer at Potomac, when micromachining the part with a CNC micromill with a 50,000-rpm spindle and an Excimer laser, the company tried various workholders, such as mechanical fixtures and water-soluble glues, before finding the answer in a workholding product from Mitee-Bite Products LLC, Center Ossipee, N.H.
“Amir contacted us regarding a process machining very small parts they wished to improve upon,” said Andrew Arsenault, marketing and sales assistant at Mitee-Bite. “They experimented with a number of options, but were unable to find a solution producing consistent results. They found our Mitee-Grip compound online and were intrigued by what this material might be able to provide. We sent samples and recommendations for use and Potomac grabbed the ball and developed an innovative design encapsulating their material in the Mitee-Grip compound, capturing the entire part and allowing intricate operations without part movement or distortion.”
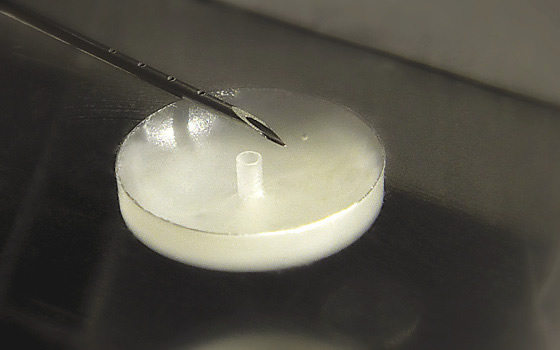
The polymeric micropart fixtured in its polymer plate using Mitee-Grip compound from Mitee-Bite Products. (Needle shown for size reference.) Image courtesy Potomac Photonics.
Mitee-Grip is a heat-activated, wax-based compound, Arsenault explained. The compound can be embedded on a paper or mesh carrier that can be ordered in 5 ' and 25 ' rolls and cut to fit the workpiece size, but Potomac opted to use the stick form. The stick can be utilized in many ways, including being melted in a pocket to capture odd shapes or added to stabilize delicate parts, providing the rigidity needed when micromachining.
“We used the stick to fill the cavity after machining half of the part, and also filled the cavity around the part within a polymer plate,” Harandi said. “By doing this, we were able to hold the part properly and machine it from the other side.”
When the compound is heated to about 225° F (107.2° C), it begins to liquefy and allows the part to sink into the compound. Once cooled, the compound hardens to securely hold the part. After machining, the compound is reheated to disengage the part.
“Using the Mitee-Grip compound made our setup time at least 20 percent faster than previous projects,” Harandi said. “The finished product was higher quality since the part was fixed more firmly while machining, and tolerances were decreased from ±20µm or greater to ±5µm. The mismatches resulting from two-sided machining almost disappeared.”
However, because the compound is wax-based, some residue typically remains after removing the part from the workholding arrangement. While this is easily removed with rubbing alcohol, Arsenault noted creativity is necessary when fixturing microparts, as well as developing a proficient cleaning method, a challenge the team at Potomac was able to meet.
“We could easily remove the residues by using a soap and water solution in an ultrasonic bath without damaging the machined parts,” Harandi said.
Related Glossary Terms
- computer numerical control ( CNC)
computer numerical control ( CNC)
Microprocessor-based controller dedicated to a machine tool that permits the creation or modification of parts. Programmed numerical control activates the machine’s servos and spindle drives and controls the various machining operations. See DNC, direct numerical control; NC, numerical control.