END USER: Box39, +7 (921) 941-85-61, www.box39.ru.
CHALLENGE: Apply modern manufacturing methods to grow a custom motorcycle business.
SOLUTION: Automate production and improve part quality and machining efficiency with a CNC machine tool and CAM software.
SOLUTION PROVIDERS: Haas Automation Inc., (800) 331-6746, www.haascnc.com; DP Technology Corp., (800) 627-8479, www.dptechnology.com.
Vladislav Belyakov had long been driven by the idea of putting together a custom motorcycle in Russia. He soon discovered the necessary components must be imported, driving up costs and delivery time. Also, there were few local companies that had the CNC machines needed to produce high-quality custom components at a reasonable price.
“In most cases, these companies had to perform time-consuming and expensive manual finishing operations,” Belyakov said. “They were unable to produce complex parts with irregular shapes, such as multiple undercuts, surface openings and transitions in different planes.”
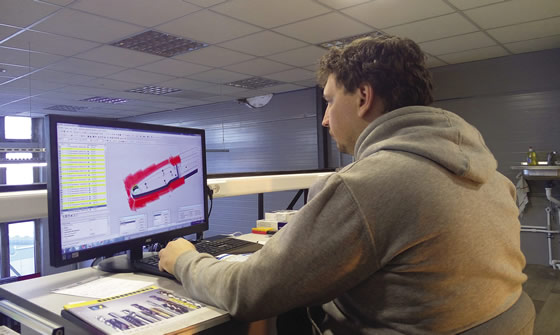
Box39 uses ESPRIT CAM software from DP Technology to program a Haas 5-axis machine. Image courtesy Box39.
Belyakov saw the manufacturing deficiencies in Russia as an opportunity to start a new business venture. He jumped from a career in financial services to motorcycle parts manufacturing in 2011 and launched Box39, a custom motorcycle shop in St. Petersburg. “Our first production facility was a rental garage,” he said. “We designed and put our first product out within 6 months of opening the doors.”
The company invested in CNC equipment to improve the quality and production efficiency of its existing products, according to Belyakov. Additionally, the new equipment would allow Box39 to develop parts with more complex geometries. After spending months evaluating different machine tools, the company purchased a Model UMC-750 5-axis universal machining center from Haas Automation Inc., Oxnard, Calif.
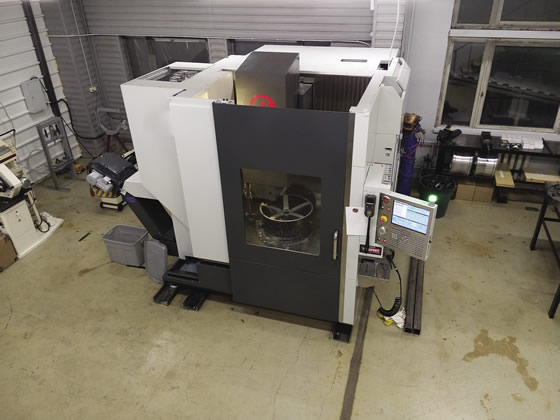
Box39 produces a custom motorcycle part on its Haas UMC-750 5-axis machining center. Image courtesy Box39.
The machine has an integrated, dual-axis trunnion table and is equipped with an inline, direct-drive, 40-taper spindle. The trunnion allows manufacturers to position parts at almost any angle for five-sided machining or to provide simultaneous 5-axis motion for contouring and complex machining.
“We chose the Haas UMC-750 to improve the quality and artistic value of our products,” Belyakov added. “This machine meets the quality standards demanded by the motorcycle market and makes it easy to work with a large tool overhang and quickly generate a lot of chips.”
After purchasing the 5-axis machine tool, the company needed CAM software to go with it and purchased an ESPRIT package from DP Technology Corp., Camarillo, Calif. “We looked for software capable of programming 3-axis and 5-axis milling that was compatible with our SolidWorks CAD software,” said Igor Bystrov, designer at Box39. “We selected ESPRIT because it includes a Haas-certified post-processor and a Haas UMC-750 virtual model. Another factor was the strong training and technical support provided by DP Technology in Russia.”
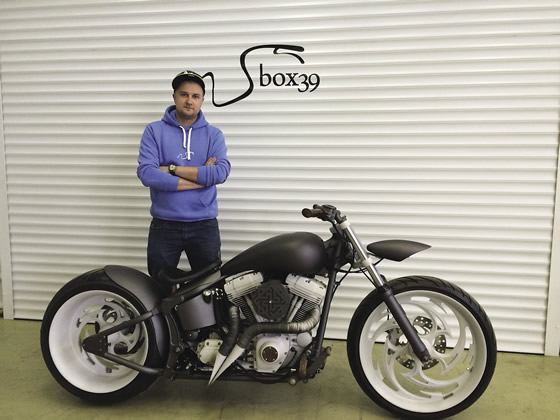
Vladislav Belyakov jumped from a career in financial services to motorcycle parts manufacturing in 2011 with Box39, a custom motorcycle shop located in St. Petersburg, Russia. Image courtesy Box39.
By late 2014, Box39 received its ESPRIT licenses and the engineers were trained on G and M codes before creating CNC programs for the Haas machine. “Since that point we have produced many CNC programs and continue to increase our programming skills,” Belyakov said. “We’re glad to have the option of viewing the simulated toolpath with this software. We use this feature every day, especially for 5-axis machining.”
These tools have already helped Box39 solve many unique challenges faster than they thought possible. “The next step will be purchasing a lathe. Without it, further development of custom components will be difficult,” Belyakov said. “This is just the beginning of our journey. The combination of a modern CNC machine and CAM software is helping us create beautiful and powerful bikes.”
Related Glossary Terms
- computer numerical control ( CNC)
computer numerical control ( CNC)
Microprocessor-based controller dedicated to a machine tool that permits the creation or modification of parts. Programmed numerical control activates the machine’s servos and spindle drives and controls the various machining operations. See DNC, direct numerical control; NC, numerical control.
- computer-aided design ( CAD)
computer-aided design ( CAD)
Product-design functions performed with the help of computers and special software.
- computer-aided manufacturing ( CAM)
computer-aided manufacturing ( CAM)
Use of computers to control machining and manufacturing processes.
- gang cutting ( milling)
gang cutting ( milling)
Machining with several cutters mounted on a single arbor, generally for simultaneous cutting.
- lathe
lathe
Turning machine capable of sawing, milling, grinding, gear-cutting, drilling, reaming, boring, threading, facing, chamfering, grooving, knurling, spinning, parting, necking, taper-cutting, and cam- and eccentric-cutting, as well as step- and straight-turning. Comes in a variety of forms, ranging from manual to semiautomatic to fully automatic, with major types being engine lathes, turning and contouring lathes, turret lathes and numerical-control lathes. The engine lathe consists of a headstock and spindle, tailstock, bed, carriage (complete with apron) and cross slides. Features include gear- (speed) and feed-selector levers, toolpost, compound rest, lead screw and reversing lead screw, threading dial and rapid-traverse lever. Special lathe types include through-the-spindle, camshaft and crankshaft, brake drum and rotor, spinning and gun-barrel machines. Toolroom and bench lathes are used for precision work; the former for tool-and-die work and similar tasks, the latter for small workpieces (instruments, watches), normally without a power feed. Models are typically designated according to their “swing,” or the largest-diameter workpiece that can be rotated; bed length, or the distance between centers; and horsepower generated. See turning machine.
- machining center
machining center
CNC machine tool capable of drilling, reaming, tapping, milling and boring. Normally comes with an automatic toolchanger. See automatic toolchanger.
- milling
milling
Machining operation in which metal or other material is removed by applying power to a rotating cutter. In vertical milling, the cutting tool is mounted vertically on the spindle. In horizontal milling, the cutting tool is mounted horizontally, either directly on the spindle or on an arbor. Horizontal milling is further broken down into conventional milling, where the cutter rotates opposite the direction of feed, or “up” into the workpiece; and climb milling, where the cutter rotates in the direction of feed, or “down” into the workpiece. Milling operations include plane or surface milling, endmilling, facemilling, angle milling, form milling and profiling.
- sawing machine ( saw)
sawing machine ( saw)
Machine designed to use a serrated-tooth blade to cut metal or other material. Comes in a wide variety of styles but takes one of four basic forms: hacksaw (a simple, rugged machine that uses a reciprocating motion to part metal or other material); cold or circular saw (powers a circular blade that cuts structural materials); bandsaw (runs an endless band; the two basic types are cutoff and contour band machines, which cut intricate contours and shapes); and abrasive cutoff saw (similar in appearance to the cold saw, but uses an abrasive disc that rotates at high speeds rather than a blade with serrated teeth).
- toolpath( cutter path)
toolpath( cutter path)
2-D or 3-D path generated by program code or a CAM system and followed by tool when machining a part.