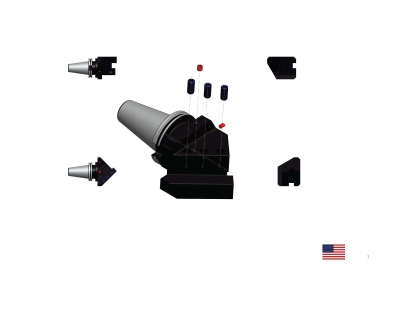
Briney Tooling Systems worked closely with a manufacturer to develop a special dual-contact, CAT 50, stick turning toolholder for an Okuma MacTurn 550 mill/turn center. The customer had some special turning stick tools that were 1.5-inches square and there was no standard for the lathe stick tools. Briney Tooling Systems was able to analyze the tool and determine the correct cutting angle required for the stick tooling and built custom adapters that ultimately saved the customer from having to reengineer its entire catalog of stick-type lathe tooling.
Many of today’s machining centers, like the Okuma MacTurn 550, are equipped with dual-contact spindles, where there is dual contact between the machine spindle taper and the toolholder taper shank. The benefit is improved rigidity that ensures accuracy and surface finish, extends tool life and minimizes deflection and vibration for high speed machining. Combine that spindle with a dual-contact toolholder and you have the best of both worlds. The dual contact of the toolholder taper shank and the toolholder flange is a method to eliminate pullback of the toolholder. The steep taper contacts the spindle taper and flange contact on the spindle face, making a solid union in both the axial and radial planes. As a result, dual contact toolholders are resistant to axial movement because the face contact prevents the toolholder from being pulled up into the spindle at high speed. Briney has been providing dual contact toolholders for many years, so applying that capability to the Okuma MacTurn lathe tooling was easily accomplished.
Contact Details
Related Glossary Terms
- centers
centers
Cone-shaped pins that support a workpiece by one or two ends during machining. The centers fit into holes drilled in the workpiece ends. Centers that turn with the workpiece are called “live” centers; those that do not are called “dead” centers.
- lathe
lathe
Turning machine capable of sawing, milling, grinding, gear-cutting, drilling, reaming, boring, threading, facing, chamfering, grooving, knurling, spinning, parting, necking, taper-cutting, and cam- and eccentric-cutting, as well as step- and straight-turning. Comes in a variety of forms, ranging from manual to semiautomatic to fully automatic, with major types being engine lathes, turning and contouring lathes, turret lathes and numerical-control lathes. The engine lathe consists of a headstock and spindle, tailstock, bed, carriage (complete with apron) and cross slides. Features include gear- (speed) and feed-selector levers, toolpost, compound rest, lead screw and reversing lead screw, threading dial and rapid-traverse lever. Special lathe types include through-the-spindle, camshaft and crankshaft, brake drum and rotor, spinning and gun-barrel machines. Toolroom and bench lathes are used for precision work; the former for tool-and-die work and similar tasks, the latter for small workpieces (instruments, watches), normally without a power feed. Models are typically designated according to their “swing,” or the largest-diameter workpiece that can be rotated; bed length, or the distance between centers; and horsepower generated. See turning machine.
- shank
shank
Main body of a tool; the portion of a drill or similar end-held tool that fits into a collet, chuck or similar mounting device.
- toolholder
toolholder
Secures a cutting tool during a machining operation. Basic types include block, cartridge, chuck, collet, fixed, modular, quick-change and rotating.
- turning
turning
Workpiece is held in a chuck, mounted on a face plate or secured between centers and rotated while a cutting tool, normally a single-point tool, is fed into it along its periphery or across its end or face. Takes the form of straight turning (cutting along the periphery of the workpiece); taper turning (creating a taper); step turning (turning different-size diameters on the same work); chamfering (beveling an edge or shoulder); facing (cutting on an end); turning threads (usually external but can be internal); roughing (high-volume metal removal); and finishing (final light cuts). Performed on lathes, turning centers, chucking machines, automatic screw machines and similar machines.