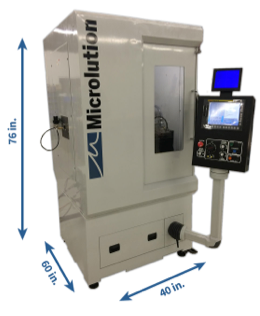
Microlution Inc., Chicago, recently introduced its MR-4 Precision Micro Lathe turning platform that reportedly offers positional accuracy of +/-0.00004" (1µm), maximum acceleration better than 2g, spindle speeds up to 15,000 rpm, tooling speeds up to 30,000 rpm and torque up to 6 Nm (S1), according to the company's website.
The precision-optimized micro lathe also is said to be capable of rotational accuracy up to 75 arc-sec (with an option for < 35 arc-sec). The working volume of the machine, which offers a 360° continuous rotary axis, is 11.81" in the X axis, 4.92" in the Y axis and 5.91" in the Z axis.
With a 40" x 60" footprint and a modular design, the MR-4 is said to be suitable for multiple configurations, and combines gang-style tooling and Swiss-style precision.
Contact Details
Related Glossary Terms
- lathe
lathe
Turning machine capable of sawing, milling, grinding, gear-cutting, drilling, reaming, boring, threading, facing, chamfering, grooving, knurling, spinning, parting, necking, taper-cutting, and cam- and eccentric-cutting, as well as step- and straight-turning. Comes in a variety of forms, ranging from manual to semiautomatic to fully automatic, with major types being engine lathes, turning and contouring lathes, turret lathes and numerical-control lathes. The engine lathe consists of a headstock and spindle, tailstock, bed, carriage (complete with apron) and cross slides. Features include gear- (speed) and feed-selector levers, toolpost, compound rest, lead screw and reversing lead screw, threading dial and rapid-traverse lever. Special lathe types include through-the-spindle, camshaft and crankshaft, brake drum and rotor, spinning and gun-barrel machines. Toolroom and bench lathes are used for precision work; the former for tool-and-die work and similar tasks, the latter for small workpieces (instruments, watches), normally without a power feed. Models are typically designated according to their “swing,” or the largest-diameter workpiece that can be rotated; bed length, or the distance between centers; and horsepower generated. See turning machine.
- lathe turning
lathe turning
Machining operation in which a workpiece is rotated, while a cutting tool removes material, either externally or internally.
- modular design ( modular construction)
modular design ( modular construction)
Manufacturing of a product in subassemblies that permits fast and simple replacement of defective assemblies and tailoring of the product for different purposes. See interchangeable parts.
- turning
turning
Workpiece is held in a chuck, mounted on a face plate or secured between centers and rotated while a cutting tool, normally a single-point tool, is fed into it along its periphery or across its end or face. Takes the form of straight turning (cutting along the periphery of the workpiece); taper turning (creating a taper); step turning (turning different-size diameters on the same work); chamfering (beveling an edge or shoulder); facing (cutting on an end); turning threads (usually external but can be internal); roughing (high-volume metal removal); and finishing (final light cuts). Performed on lathes, turning centers, chucking machines, automatic screw machines and similar machines.