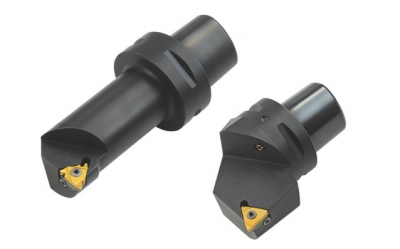
Carmexʼs quick-change polygon threading toolholders enable customers whose machines are equipped with the Sandvik Capto system to utilize Carmexʼs threading inserts. Incorporating a polygon taper to ensure automatic radial centering and even pressure around the coupling, the toolholders are ISO standard (26623) compliant for toolholding systems. The 1.4-degree tapered polygon shank speeds tool changing, and the toolholders are available in configurations for external and internal threading operations.
Jeff Dei, president of Carmex USA, comments, “Customers that have equipped their machines with the Capto system now have the opportunity to incorporate Carmexʼs superior turning technology with the toolholder that is both easy to change and compatible with Capto and other systems. The centering capability and precise fit make this system the ideal choice for precision turning operations in tough materials.”
Contact Details
Related Glossary Terms
- centering
centering
1. Process of locating the center of a workpiece to be mounted on centers. 2. Process of mounting the workpiece concentric to the machine spindle. See centers.
- shank
shank
Main body of a tool; the portion of a drill or similar end-held tool that fits into a collet, chuck or similar mounting device.
- threading
threading
Process of both external (e.g., thread milling) and internal (e.g., tapping, thread milling) cutting, turning and rolling of threads into particular material. Standardized specifications are available to determine the desired results of the threading process. Numerous thread-series designations are written for specific applications. Threading often is performed on a lathe. Specifications such as thread height are critical in determining the strength of the threads. The material used is taken into consideration in determining the expected results of any particular application for that threaded piece. In external threading, a calculated depth is required as well as a particular angle to the cut. To perform internal threading, the exact diameter to bore the hole is critical before threading. The threads are distinguished from one another by the amount of tolerance and/or allowance that is specified. See turning.
- toolholder
toolholder
Secures a cutting tool during a machining operation. Basic types include block, cartridge, chuck, collet, fixed, modular, quick-change and rotating.
- turning
turning
Workpiece is held in a chuck, mounted on a face plate or secured between centers and rotated while a cutting tool, normally a single-point tool, is fed into it along its periphery or across its end or face. Takes the form of straight turning (cutting along the periphery of the workpiece); taper turning (creating a taper); step turning (turning different-size diameters on the same work); chamfering (beveling an edge or shoulder); facing (cutting on an end); turning threads (usually external but can be internal); roughing (high-volume metal removal); and finishing (final light cuts). Performed on lathes, turning centers, chucking machines, automatic screw machines and similar machines.