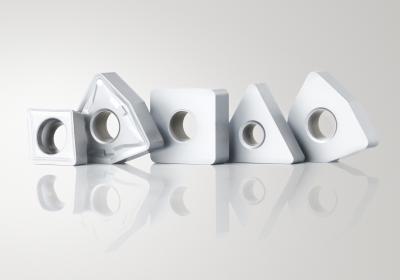
Seco’s new TK1501 and TK0501 insert grades incorporate the latest developments in next-generation Duratomic coating technology. The new dedicated cast iron turning grades reach a new level of toughness and wear
resistance, as well as reduce tool waste and process more parts per edge.
With the latest Duratomic coating technology, these new grades have a wider application range and an overall increase in tool life and productivity. Seco’s exclusive Duratomic process manipulates aluminum and oxygen at the atomic level to create insert coatings with unmatched toughness and abrasion resistance. Their balance of
toughness and hardness meets the highest performance demands consistently and reliably.
TK1501 and TK0501 integrate Seco’s EDGE INTELLIGENCE concept that combines extensive high-performance insert experience and knowledge in every cutting edge for every application requirement. Chrome Used-Edge Detection makes it easy to tell if an insert’s cutting edges have made contact with a workpiece. The inserts are optimized to
provide the highest possible contrast to make it easy to instantly identify when an edge has been used, even in low-light environments. TK1501 and TK0501 grades’ Chrome Used-Edge Detection contributes to a potential 30 percent decrease in waste due to prematurely discarded inserts.
The inserts’ ability to increase productivity through higher speeds and feed rates reduces lead times as well as run-in and setup times. This results in a decreased chance of encountering production bottle necks on a shop’s turning machines. The new grades are available in a comprehensive selection of geometries—from roughing to finishing—to give end users a desirable surface finish in any application.
Contact Details
Related Glossary Terms
- feed
feed
Rate of change of position of the tool as a whole, relative to the workpiece while cutting.
- hardness
hardness
Hardness is a measure of the resistance of a material to surface indentation or abrasion. There is no absolute scale for hardness. In order to express hardness quantitatively, each type of test has its own scale, which defines hardness. Indentation hardness obtained through static methods is measured by Brinell, Rockwell, Vickers and Knoop tests. Hardness without indentation is measured by a dynamic method, known as the Scleroscope test.
- turning
turning
Workpiece is held in a chuck, mounted on a face plate or secured between centers and rotated while a cutting tool, normally a single-point tool, is fed into it along its periphery or across its end or face. Takes the form of straight turning (cutting along the periphery of the workpiece); taper turning (creating a taper); step turning (turning different-size diameters on the same work); chamfering (beveling an edge or shoulder); facing (cutting on an end); turning threads (usually external but can be internal); roughing (high-volume metal removal); and finishing (final light cuts). Performed on lathes, turning centers, chucking machines, automatic screw machines and similar machines.
- wear resistance
wear resistance
Ability of the tool to withstand stresses that cause it to wear during cutting; an attribute linked to alloy composition, base material, thermal conditions, type of tooling and operation and other variables.