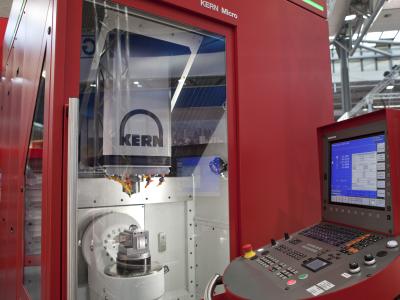
Kern Precision says its Micro five-axis milling machine does not only tout its reliability and precision, but also the size of its footprint, the capacity of its palletized toolchanger, its plug-and-play capability, its power and its versatility in terms of the size of workpiece it can accommodate.
“In general, the ultra-high precision milling market, where high productivity and precision are key, lacked a highly reliable five-axis machining solution,” says Gary Zurek, Kern’s sales manager. “The combination of high productivity and achieving ultra-high precision on five-axis and three-plus-two axis parts has always been challenging to manufacturers.”
The KERN Micro offers manufacturers a diversified 5-axis machine that can bridge the gap among milling technologies, including high-speed machining, hard milling, graphite milling and micromilling, he says.
With its rectangular footprint, occupying just shy of 5 feet x 10 feet on the shop floor, the KERN Micro not only has a smaller footprint, the slim design means several machines can be lined up like row houses with other Micros for a highly automated work system.
“In today’s economic climate, shop real estate is very expensive,” says Zurek. “Doing more in a KERN Micro is a prized attribute, but if a machine is taking up a lot of shop space then that can be a negative factor.”
If the Micro is small, its palletized toolchanger is just the opposite. The machine’s tool cabinet is large enough to hold up to 209 tools and convenient to use because of its glass front. Quick-change tool pallets can be assembled for individual jobs and stored separately.
“For years now, the industry has recognized the advantages of modular fixturing and management in automated situations,” says Matthias Fritz, KERN’s R&D manager, adding that tool management can be a stumbling block in a highly productive environment. “Kern has applied this same technology to managing tool holders by palletizing them and managing them directly on the control.”
The advantage is an easily managed and trouble-free system that contributes to the efficiency of the entire production cycle by significantly reducing setup times.
Not only tool changing, but also setting up the Micro is fast.
It’s designed to be plug-and-play, with four connections required during setup for the machine, whose units are almost fully integrated: An optional water chiller is a standalone component. The cooling system is another master piece of Fritz. All relevant parts like spindle, axes and motor flunch are individually cooled and controlled. The cooling system is basically a heat exchanger and with the chiller being outside the machine there is no waste heat inside the machine. With temperature being a major issue for accuracy especially in production cycles, this solution is simply ingenious.
With its HSK 40 spindle with internal coolant lubrication, not only can shops achieve micron-level precision on micro-size parts, they can also cut more than 70 lbs. of steel in an hour. An HSK 25 spindle is available as an option.
Further, due to an integrated fourth and fifth axis table in a traveling column machine design, the Micro can handle workpieces up to almost 14 inches in diameter. The intelligent arrangement of the fourth and fifth axes results in a large swivel range that allows full use of the working area.
Contact Details
Related Glossary Terms
- coolant
coolant
Fluid that reduces temperature buildup at the tool/workpiece interface during machining. Normally takes the form of a liquid such as soluble or chemical mixtures (semisynthetic, synthetic) but can be pressurized air or other gas. Because of water’s ability to absorb great quantities of heat, it is widely used as a coolant and vehicle for various cutting compounds, with the water-to-compound ratio varying with the machining task. See cutting fluid; semisynthetic cutting fluid; soluble-oil cutting fluid; synthetic cutting fluid.
- gang cutting ( milling)
gang cutting ( milling)
Machining with several cutters mounted on a single arbor, generally for simultaneous cutting.
- milling
milling
Machining operation in which metal or other material is removed by applying power to a rotating cutter. In vertical milling, the cutting tool is mounted vertically on the spindle. In horizontal milling, the cutting tool is mounted horizontally, either directly on the spindle or on an arbor. Horizontal milling is further broken down into conventional milling, where the cutter rotates opposite the direction of feed, or “up” into the workpiece; and climb milling, where the cutter rotates in the direction of feed, or “down” into the workpiece. Milling operations include plane or surface milling, endmilling, facemilling, angle milling, form milling and profiling.
- milling machine ( mill)
milling machine ( mill)
Runs endmills and arbor-mounted milling cutters. Features include a head with a spindle that drives the cutters; a column, knee and table that provide motion in the three Cartesian axes; and a base that supports the components and houses the cutting-fluid pump and reservoir. The work is mounted on the table and fed into the rotating cutter or endmill to accomplish the milling steps; vertical milling machines also feed endmills into the work by means of a spindle-mounted quill. Models range from small manual machines to big bed-type and duplex mills. All take one of three basic forms: vertical, horizontal or convertible horizontal/vertical. Vertical machines may be knee-type (the table is mounted on a knee that can be elevated) or bed-type (the table is securely supported and only moves horizontally). In general, horizontal machines are bigger and more powerful, while vertical machines are lighter but more versatile and easier to set up and operate.
- modular fixturing
modular fixturing
System in which fixtures are constructed from standardized, reusable components. Fixtures are assembled and disassembled quickly. Basic styles are subplate, dowel-pin and T-slot. See fixture; modular tooling.
- toolchanger
toolchanger
Carriage or drum attached to a machining center that holds tools until needed; when a tool is needed, the toolchanger inserts the tool into the machine spindle. See automatic toolchanger.