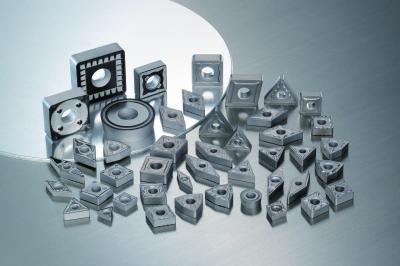
New from Sumitomo Electric Carbide Inc., AC8000P Series Grades for steel turning features advanced Absotech Platinum CVD Coating for a longer tool life and an overall cost reduction in steel cutting. For exceptional performance, the AC8000P series consists of this patented CVD coating, a new surface layer and a smooth surface treatment from the crystal orientation process.
Three grades are available to meet a complete range of application requirements. The AC8015P grade offers superior wear resistance during high-speed, high-efficiency steel cutting. Its edge treatment and newly developed coating result in twice the crater wear resistance compared to conventional grades, according to the company. The AC8025P grade is exceptionally reliable during general-purpose steel cutting. Its special surface treatment results in improved tool surface smoothness, as well as adhesion and chipping resistance two times better than traditional grades. The AC8035P grade provides excellent stability during interrupted steel cutting. Its special surface treatment drastically reduces tensile residual stress in coating for twice the fracture resistance of standard grades.
The wide range of applications for the AC8000P grade includes ring gears, CVT parts, toolholders, axle ends, bushings, flanges and gears. Some chipbreaker suggestions include the EGU, the EGE and the EUX.
Contact Details
Related Glossary Terms
- chemical vapor deposition ( CVD)
chemical vapor deposition ( CVD)
High-temperature (1,000° C or higher), atmosphere-controlled process in which a chemical reaction is induced for the purpose of depositing a coating 2µm to 12µm thick on a tool’s surface. See coated tools; PVD, physical vapor deposition.
- chipbreaker
chipbreaker
Groove or other tool geometry that breaks chips into small fragments as they come off the workpiece. Designed to prevent chips from becoming so long that they are difficult to control, catch in turning parts and cause safety problems.
- residual stress
residual stress
Stress present in a body that is free of external forces or thermal gradients.
- turning
turning
Workpiece is held in a chuck, mounted on a face plate or secured between centers and rotated while a cutting tool, normally a single-point tool, is fed into it along its periphery or across its end or face. Takes the form of straight turning (cutting along the periphery of the workpiece); taper turning (creating a taper); step turning (turning different-size diameters on the same work); chamfering (beveling an edge or shoulder); facing (cutting on an end); turning threads (usually external but can be internal); roughing (high-volume metal removal); and finishing (final light cuts). Performed on lathes, turning centers, chucking machines, automatic screw machines and similar machines.
- wear resistance
wear resistance
Ability of the tool to withstand stresses that cause it to wear during cutting; an attribute linked to alloy composition, base material, thermal conditions, type of tooling and operation and other variables.