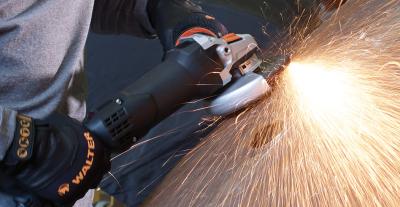
Walter Surface Technologies has introduced two heavy-duty grinders: the Ironman and Ironman PS. Designed for strenuous, prolonged use, the Ironman and Ironman PS feature an ergonomic rat-tail design, perfect balance, 1,750 watts of power, 6-inch wheel capacity, a QUICK-R instant release function, and the Walter Stabilizer, which reduces vibration and extends the life and productivity of abrasives by up to 30 percent.
The Ironman PS offers the same durability and high performance as the Ironman, but with added safety features. Its “deadman” switch and mechanical brake stop grinding wheels from turning within 2 seconds of relieving the trigger, and cutting wheels within 1.5 seconds, thus minimizing workplace risks and offering users even greater safety.
“The Ironman and Ironman PS grinders are our most powerful, most productive heavy-duty grinders with 6” wheel capacity,” says Ryan Boyd, product manager of tooling and power tools at Walter Surface Technologies. “Their physical design, power, and cutting-edge features make them the perfect tool for the most demanding jobs—and the best heavy-duty grinders in the marketplace.”
Built to meet the large-scale needs and exacting standards of the aerospace, military, naval, energy, transportation and other industries and sectors, Ironman heavy-duty grinders can be used in a range of grinding and cutting operations.
Contact Details
Related Glossary Terms
- grinding
grinding
Machining operation in which material is removed from the workpiece by a powered abrasive wheel, stone, belt, paste, sheet, compound, slurry, etc. Takes various forms: surface grinding (creates flat and/or squared surfaces); cylindrical grinding (for external cylindrical and tapered shapes, fillets, undercuts, etc.); centerless grinding; chamfering; thread and form grinding; tool and cutter grinding; offhand grinding; lapping and polishing (grinding with extremely fine grits to create ultrasmooth surfaces); honing; and disc grinding.
- turning
turning
Workpiece is held in a chuck, mounted on a face plate or secured between centers and rotated while a cutting tool, normally a single-point tool, is fed into it along its periphery or across its end or face. Takes the form of straight turning (cutting along the periphery of the workpiece); taper turning (creating a taper); step turning (turning different-size diameters on the same work); chamfering (beveling an edge or shoulder); facing (cutting on an end); turning threads (usually external but can be internal); roughing (high-volume metal removal); and finishing (final light cuts). Performed on lathes, turning centers, chucking machines, automatic screw machines and similar machines.