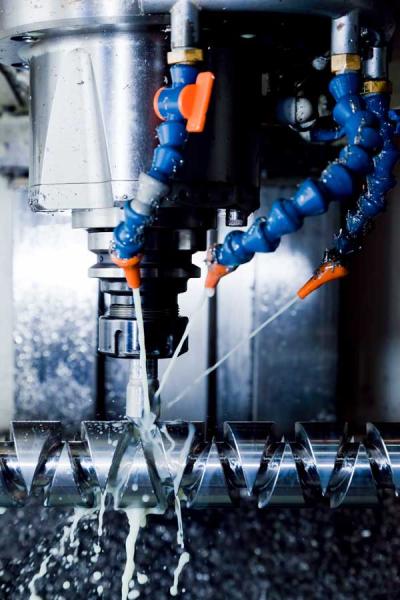
Tech Cool 35058 is a unique premium machining fluid developed specifically for applications requiring superior microfinish on ferrous alloys; low- and high-carbon steels, titanium, molybdenum and tough alloys. It is low foaming and specially formulated to run longer in high velocity central systems. The product offers enhanced corrosion protection, contains no chlorine, sulfur, boron or phosphorus compounds and is compatible with ferrous and aluminum alloys. The technology uses a unique blend of additives which delivers extended sump life. Tech Cool 35058 is recommended for use in most medium to heavy duty machining and grinding applications.
Tech Cool 35037 is a distinctive general-purpose machining and grinding fluid developed specifically for applications requiring efficient and economical performance on aluminum and copper alloys. It is low foaming and designed to deliver superior finishes for aluminum drilling and tapping applications. The product offers excellent corrosion protection, extended sump life and contains no sulfur compounds. Its unique lubricity is activated by a chlorinated EP ingredient. It. Tech Cool 35037 is completely free of formaldehyde releasing biocides, and recommended for use in most general-purpose machining and grinding applications.
Both Tech Cool 35058 and 35037 exhibit enhanced hard water tolerance and increased emulsion stability. The in-service cleanliness of these products allows for long-term system life without the formation of heavy, tacky, water insoluble residues.
Contact Details
Related Glossary Terms
- alloys
alloys
Substances having metallic properties and being composed of two or more chemical elements of which at least one is a metal.
- aluminum alloys
aluminum alloys
Aluminum containing specified quantities of alloying elements added to obtain the necessary mechanical and physical properties. Aluminum alloys are divided into two categories: wrought compositions and casting compositions. Some compositions may contain up to 10 alloying elements, but only one or two are the main alloying elements, such as copper, manganese, silicon, magnesium, zinc or tin.
- copper alloys
copper alloys
Copper containing specified quantities of alloying elements added to obtain the necessary mechanical and physical properties. The most common copper alloys are divided into six groups, and each group contains one of the following major alloying elements: brasses—major alloying element is zinc; phosphor bronzes—major alloying element is tin; aluminum bronzes—major alloying element is aluminum; silicon bronzes—major alloying element is silicon; copper-nickels and nickel-silvers—major alloying element is nickel; and dilute-copper or high-copper alloys, which contain small amounts of various elements such as beryllium, cadmium, chromium or iron.
- emulsion
emulsion
Suspension of one liquid in another, such as oil in water.
- extreme pressure additives ( EP)
extreme pressure additives ( EP)
Cutting-fluid additives (chlorine, sulfur or phosphorus compounds) that chemically react with the workpiece material to minimize chipwelding. Good for high-speed machining. See cutting fluid.
- grinding
grinding
Machining operation in which material is removed from the workpiece by a powered abrasive wheel, stone, belt, paste, sheet, compound, slurry, etc. Takes various forms: surface grinding (creates flat and/or squared surfaces); cylindrical grinding (for external cylindrical and tapered shapes, fillets, undercuts, etc.); centerless grinding; chamfering; thread and form grinding; tool and cutter grinding; offhand grinding; lapping and polishing (grinding with extremely fine grits to create ultrasmooth surfaces); honing; and disc grinding.
- lubricity
lubricity
Measure of the relative efficiency with which a cutting fluid or lubricant reduces friction between surfaces.
- metalworking
metalworking
Any manufacturing process in which metal is processed or machined such that the workpiece is given a new shape. Broadly defined, the term includes processes such as design and layout, heat-treating, material handling and inspection.
- tapping
tapping
Machining operation in which a tap, with teeth on its periphery, cuts internal threads in a predrilled hole having a smaller diameter than the tap diameter. Threads are formed by a combined rotary and axial-relative motion between tap and workpiece. See tap.
- tolerance
tolerance
Minimum and maximum amount a workpiece dimension is allowed to vary from a set standard and still be acceptable.