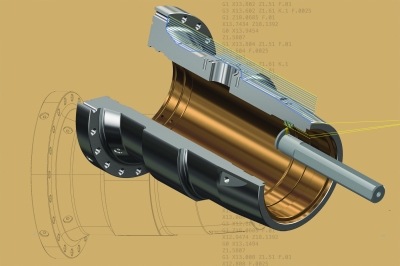
From accepting and programming any CAD file to Dynamic roughing and precision finishing, Mastercam 2019 Lathe gives you a variety of techniques to turn all of your parts exactly as you need them. Mastercam 2019 Lathe features a new Tool Designer, Mill-Turn Environments and Multiple Plunge.
Build tools from 3D STEP models using the new Tool Designer. The Tool Designer is a function panel with tab-style navigation, providing a structured workflow that is similar to using a wizard. You can define tools, assign them to operations, and view them when running Classic Backplot and Mastercam Simulator.
Mastercam 2019 allows Lathe users to run select Mill-Turn machine environments, giving users the productivity benefits of Mastercam’s Mill-Turn programming environment. Experience automated job setup and part transfer, full machine simulation, and simplified programming of C/Y axis toolpaths.
The Lathe Groove toolpath includes a Multiple Plunge option, which allows you to rough out a groove with rib cuts. This is beneficial when you are concerned about tool deflection. Consistent tool pressure can result in better chip control, and more even tool wear. Multiple Plunge gives you the option to machine the ribs with a more aggressive feed rate than the initial plunges.
Also available in the Mastercam 2019 Lathe is:
- Improved support for cross-centerline turning.
- Support for Swiss machines. Swiss users with active Lathe and Mill/Mill 3D licenses can now take advantage of familiar Lathe and Mill toolpaths (available in the United States).
- Full integration of the PrimeTurning toolpath. Mastercam 2019 features improved tool libraries, including 3D tool libraries and the introduction of 3D tool support.
Contact Details
Related Glossary Terms
- computer-aided design ( CAD)
computer-aided design ( CAD)
Product-design functions performed with the help of computers and special software.
- feed
feed
Rate of change of position of the tool as a whole, relative to the workpiece while cutting.
- lathe
lathe
Turning machine capable of sawing, milling, grinding, gear-cutting, drilling, reaming, boring, threading, facing, chamfering, grooving, knurling, spinning, parting, necking, taper-cutting, and cam- and eccentric-cutting, as well as step- and straight-turning. Comes in a variety of forms, ranging from manual to semiautomatic to fully automatic, with major types being engine lathes, turning and contouring lathes, turret lathes and numerical-control lathes. The engine lathe consists of a headstock and spindle, tailstock, bed, carriage (complete with apron) and cross slides. Features include gear- (speed) and feed-selector levers, toolpost, compound rest, lead screw and reversing lead screw, threading dial and rapid-traverse lever. Special lathe types include through-the-spindle, camshaft and crankshaft, brake drum and rotor, spinning and gun-barrel machines. Toolroom and bench lathes are used for precision work; the former for tool-and-die work and similar tasks, the latter for small workpieces (instruments, watches), normally without a power feed. Models are typically designated according to their “swing,” or the largest-diameter workpiece that can be rotated; bed length, or the distance between centers; and horsepower generated. See turning machine.
- milling machine ( mill)
milling machine ( mill)
Runs endmills and arbor-mounted milling cutters. Features include a head with a spindle that drives the cutters; a column, knee and table that provide motion in the three Cartesian axes; and a base that supports the components and houses the cutting-fluid pump and reservoir. The work is mounted on the table and fed into the rotating cutter or endmill to accomplish the milling steps; vertical milling machines also feed endmills into the work by means of a spindle-mounted quill. Models range from small manual machines to big bed-type and duplex mills. All take one of three basic forms: vertical, horizontal or convertible horizontal/vertical. Vertical machines may be knee-type (the table is mounted on a knee that can be elevated) or bed-type (the table is securely supported and only moves horizontally). In general, horizontal machines are bigger and more powerful, while vertical machines are lighter but more versatile and easier to set up and operate.
- toolpath( cutter path)
toolpath( cutter path)
2-D or 3-D path generated by program code or a CAM system and followed by tool when machining a part.
- turning
turning
Workpiece is held in a chuck, mounted on a face plate or secured between centers and rotated while a cutting tool, normally a single-point tool, is fed into it along its periphery or across its end or face. Takes the form of straight turning (cutting along the periphery of the workpiece); taper turning (creating a taper); step turning (turning different-size diameters on the same work); chamfering (beveling an edge or shoulder); facing (cutting on an end); turning threads (usually external but can be internal); roughing (high-volume metal removal); and finishing (final light cuts). Performed on lathes, turning centers, chucking machines, automatic screw machines and similar machines.