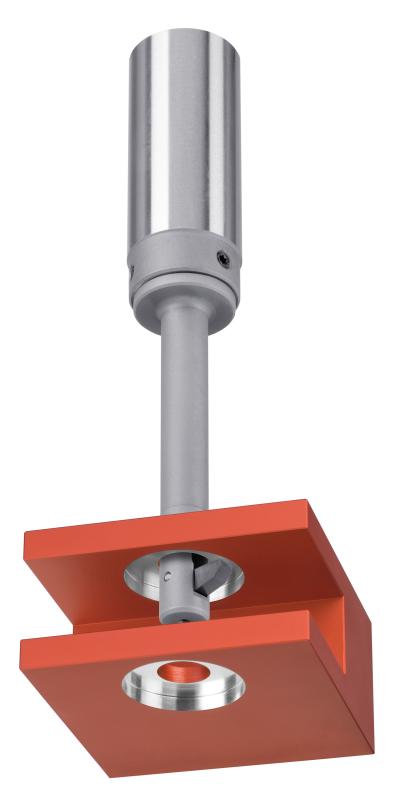
HEULE's BSF tool is for automated high-volume back spotfacing applications. The BSF tool, suitable for counterbores up to 2.3 times diameter and ranging in size from 6.5mm to 20.5mm (0.256” to 0.807”), is sold standard-stock, shipped the next day from the Cincinnati warehouse.
This unique tooling works without an antirotation device, change of spindle direction or any machine adaptations, allowing components to be spot faced in the same direction as the bore is drilled. This saves the time and cost of turning the workpiece, while allowing the spot facing of difficult to reach areas like yoke forks and screw-head countersinks.
The blade expands using centrifugal force when activating the spindle, and retracts from coolant pressure, which moves a piston to depress a pin which retracts the closed blade into the housing. The simple swing mechanism combined with the internal coolant pressure system yields optimal cutting performance, resulting in consistent spotfacing and fewer scrapped parts.
The tool works both vertically and horizontally, with replaceable carbide-coated blades for extended tool life. The tools are ideal for gear housings, yokes, engine casings and other parts in a wide range of materials.
Contact Details
Related Glossary Terms
- coolant
coolant
Fluid that reduces temperature buildup at the tool/workpiece interface during machining. Normally takes the form of a liquid such as soluble or chemical mixtures (semisynthetic, synthetic) but can be pressurized air or other gas. Because of water’s ability to absorb great quantities of heat, it is widely used as a coolant and vehicle for various cutting compounds, with the water-to-compound ratio varying with the machining task. See cutting fluid; semisynthetic cutting fluid; soluble-oil cutting fluid; synthetic cutting fluid.
- spotfacing
spotfacing
Similar to counterboring except that, in spotfacing, material around the original hole is cut. Application example: the recessed area into which a washer fits. See counterboring; countersinking.
- turning
turning
Workpiece is held in a chuck, mounted on a face plate or secured between centers and rotated while a cutting tool, normally a single-point tool, is fed into it along its periphery or across its end or face. Takes the form of straight turning (cutting along the periphery of the workpiece); taper turning (creating a taper); step turning (turning different-size diameters on the same work); chamfering (beveling an edge or shoulder); facing (cutting on an end); turning threads (usually external but can be internal); roughing (high-volume metal removal); and finishing (final light cuts). Performed on lathes, turning centers, chucking machines, automatic screw machines and similar machines.