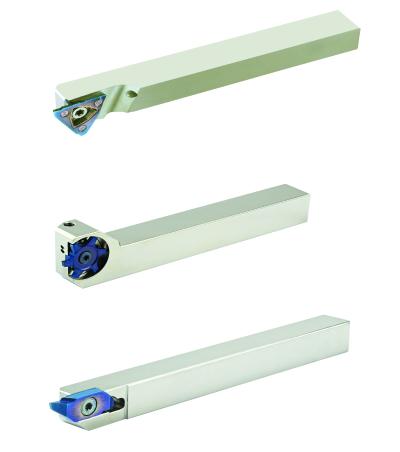
Carmex Precision Tools Ltd. has made four additions to its family of tools for Swiss-style machining applications, including the multifunction G6 six-edge turning insert designed to fit a single holder and capable of high productivity in applications, including threading, grooving, parting, and back and front turning.
The Swiss-Line inserts and toolholders, designed for parting, grooving, profiling and chamfering in mass production operations, feature PVD triple coating for high wear and heat resistance. The Swiss-Line polygon, for turning, back turning, parting, grooving, full-radius grooving and threading allows multiple inserts to be used with the same
toolholder.
The company's selection of specialized inserts for thread turning—UN or UNJ—can be used for internal or external threading. Manufactured of high-grade carbide, the inserts are multicoated for maximum performance. They include BMA-general purpose inserts, BLU-for use with Ti and stainless steel, and HBA-for hardened materials and super alloys.
According to Jim White, national sales manager for Carmex USA, “Carmex is answering the increasing demand for Swiss-type tooling by providing tools that combine high precision with flexibility. Our coated inserts have been specially developed for maximum performance in specific applications and deliver both improved surface quality and longer life. We look forward to introducing more shops and OEMs to these unique tooling configurations and quality inserts at significant savings.”
Contact Details
Related Glossary Terms
- alloys
alloys
Substances having metallic properties and being composed of two or more chemical elements of which at least one is a metal.
- chamfering
chamfering
Machining a bevel on a workpiece or tool; improves a tool’s entrance into the cut.
- grooving
grooving
Machining grooves and shallow channels. Example: grooving ball-bearing raceways. Typically performed by tools that are capable of light cuts at high feed rates. Imparts high-quality finish.
- parting
parting
When used in lathe or screw-machine operations, this process separates a completed part from chuck-held or collet-fed stock by means of a very narrow, flat-end cutting, or parting, tool.
- physical vapor deposition ( PVD)
physical vapor deposition ( PVD)
Tool-coating process performed at low temperature (500° C), compared to chemical vapor deposition (1,000° C). Employs electric field to generate necessary heat for depositing coating on a tool’s surface. See CVD, chemical vapor deposition.
- profiling
profiling
Machining vertical edges of workpieces having irregular contours; normally performed with an endmill in a vertical spindle on a milling machine or with a profiler, following a pattern. See mill, milling machine.
- threading
threading
Process of both external (e.g., thread milling) and internal (e.g., tapping, thread milling) cutting, turning and rolling of threads into particular material. Standardized specifications are available to determine the desired results of the threading process. Numerous thread-series designations are written for specific applications. Threading often is performed on a lathe. Specifications such as thread height are critical in determining the strength of the threads. The material used is taken into consideration in determining the expected results of any particular application for that threaded piece. In external threading, a calculated depth is required as well as a particular angle to the cut. To perform internal threading, the exact diameter to bore the hole is critical before threading. The threads are distinguished from one another by the amount of tolerance and/or allowance that is specified. See turning.
- toolholder
toolholder
Secures a cutting tool during a machining operation. Basic types include block, cartridge, chuck, collet, fixed, modular, quick-change and rotating.
- turning
turning
Workpiece is held in a chuck, mounted on a face plate or secured between centers and rotated while a cutting tool, normally a single-point tool, is fed into it along its periphery or across its end or face. Takes the form of straight turning (cutting along the periphery of the workpiece); taper turning (creating a taper); step turning (turning different-size diameters on the same work); chamfering (beveling an edge or shoulder); facing (cutting on an end); turning threads (usually external but can be internal); roughing (high-volume metal removal); and finishing (final light cuts). Performed on lathes, turning centers, chucking machines, automatic screw machines and similar machines.