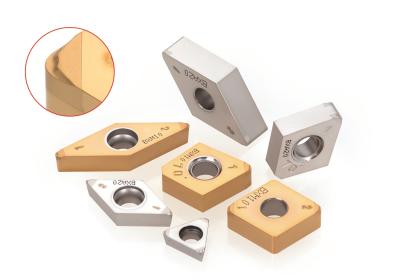
Tungaloy expands its -HP geometry line of T-CBN inserts that ensures effective chip control in finish turning of hardened steel parts.
The -HP geometry provides reliable chip control in finish cutting conditions at cutting depths of 0.2 mm (0.0079") or smaller, minimizing part quality damages caused by poor chip control.
Twenty-two additional –HP geometry T-CBN inserts are now available which further increases the chipbreaker application range in hard turning.
At a Glance
Innovative chip former ensures good chip breakage and smooth chip control
Free cutting geometry eliminates bar deflection and vibration during machining
Built-in wiper ensures better surface quality and chip control
Available in BXM10 for continuous cut and BXA20 for interrupted cut
Total of 22 inserts to be added
Contact Details
Related Glossary Terms
- chipbreaker
chipbreaker
Groove or other tool geometry that breaks chips into small fragments as they come off the workpiece. Designed to prevent chips from becoming so long that they are difficult to control, catch in turning parts and cause safety problems.
- hard turning
hard turning
Single-point cutting of a workpiece that has a hardness value higher than 45 HRC.
- interrupted cut
interrupted cut
Cutting tool repeatedly enters and exits the work. Subjects tool to shock loading, making tool toughness, impact strength and flexibility vital. Closely associated with milling operations. See shock loading.
- turning
turning
Workpiece is held in a chuck, mounted on a face plate or secured between centers and rotated while a cutting tool, normally a single-point tool, is fed into it along its periphery or across its end or face. Takes the form of straight turning (cutting along the periphery of the workpiece); taper turning (creating a taper); step turning (turning different-size diameters on the same work); chamfering (beveling an edge or shoulder); facing (cutting on an end); turning threads (usually external but can be internal); roughing (high-volume metal removal); and finishing (final light cuts). Performed on lathes, turning centers, chucking machines, automatic screw machines and similar machines.
- wiper
wiper
Metal-removing edge on the face of a cutter that travels in a plane perpendicular to the axis. It is the edge that sweeps the machined surface. The flat should be as wide as the feed per revolution of the cutter. This allows any given insert to wipe the entire workpiece surface and impart a fine surface finish at a high feed rate.