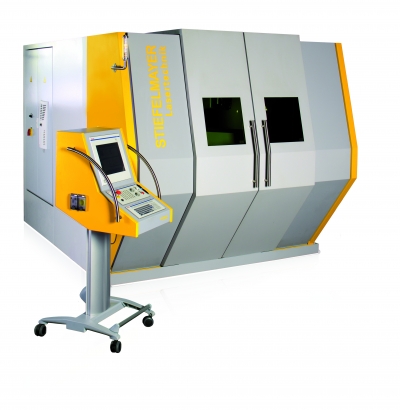
German Machine Tools of America (GMTA) proudly announces the signing of an agreement with Stiefelmayer GmbH (Denkendorf, Germany) to represent that company’s line of laser machines in North America. Stiefelmayer offers lasers for various cutting applications, including motor laminations, plus laser hardening.
The agreement is effective immediately and was announced by GMTA President Walter Friedrich from the headquarters in Ann Arbor, Michigan. Friedrich commented, “The Stiefelmayer line is a highly regarded brand in Germany. Coupled with our Arnold line of laser systems, the new lasers will give us a formidable offering to the North American market, especially in automotive and the burgeoning EV market.”
Stiefelmayer further prides itself on their blue effective® program of energy saving technology and sustainability, designed to create both environmental and economic benefits to the user.
The Stiefelmayer laser is particularly well adapted to cutting precision shapes in thin substrates, including mild steel, stainless, copper and brass. Motor laminations are a particular specialty and this fact matches the drive to EV in the American auto industry.
Contact Details
Related Glossary Terms
- arbor
arbor
Shaft used for rotary support in machining applications. In grinding, the spindle for mounting the wheel; in milling and other cutting operations, the shaft for mounting the cutter.
- hardening
hardening
Process of increasing the surface hardness of a part. It is accomplished by heating a piece of steel to a temperature within or above its critical range and then cooling (or quenching) it rapidly. In any heat-treatment operation, the rate of heating is important. Heat flows from the exterior to the interior of steel at a definite rate. If the steel is heated too quickly, the outside becomes hotter than the inside and the desired uniform structure cannot be obtained. If a piece is irregular in shape, a slow heating rate is essential to prevent warping and cracking. The heavier the section, the longer the heating time must be to achieve uniform results. Even after the correct temperature has been reached, the piece should be held at the temperature for a sufficient period of time to permit its thickest section to attain a uniform temperature. See workhardening.