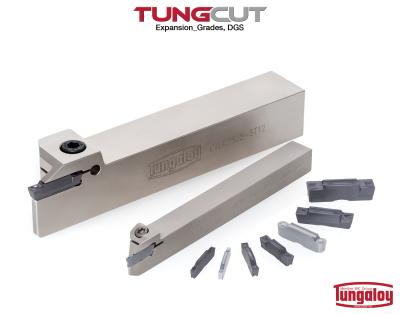
Tungaloy has added new grades and geometries to its TungCut line of grooving and parting-off tools.
A multifunctional grooving and parting-off line, TungCut offers a wide range of insert and toolholder variations that provide customers with maximum performance in OD/ID grooving, face grooving, groove turning, and parting operations. With strong and reliable insert clamping, TungCut guarantees minimum tool chatter, while providing maximum precision and tool life during heavy duty grooving such as groove turning.
Two new grades have been added to TungCut to enhance its capacity in exotic materials: AH8005 insert grade, featuring strong coating adherence to its carbide substrate, eliminates notch wear that typically occurs during the machining of heat-resistant superalloys (HRSAs). The grade boasts extraordinary wear resistance, providing long and predictable tool life during the machining of HRSAs. KS05F, a non-coated carbide grade, provides a good balance of wear resistance and fracture toughness, while eliminating built-up edge. The grade is ideal for productive groove machining of titanium alloys.
New geometries include DGS inserts with 0.05 mm and 0.10 mm (.0002″ and .0004″) corner radii. These sharp cornered inserts allow lighter cutting and precision grooving/ parting-off of small parts advantageous in Swiss machine applications. In addition, new STR insert features a full-radius, single-ended geometry for profiling. Unlike double-ended inserts, a single-ended STR eliminates concerns of the other cutting end interfering with the workpiece during machining, enabling close machining of deeper areas of the workpiece. Total of 85 items have been added to the TungCut line.
Contact Details
Related Glossary Terms
- alloys
alloys
Substances having metallic properties and being composed of two or more chemical elements of which at least one is a metal.
- built-up edge ( BUE)
built-up edge ( BUE)
1. Permanently damaging a metal by heating to cause either incipient melting or intergranular oxidation. 2. In grinding, getting the workpiece hot enough to cause discoloration or to change the microstructure by tempering or hardening.
- chatter
chatter
Condition of vibration involving the machine, workpiece and cutting tool. Once this condition arises, it is often self-sustaining until the problem is corrected. Chatter can be identified when lines or grooves appear at regular intervals in the workpiece. These lines or grooves are caused by the teeth of the cutter as they vibrate in and out of the workpiece and their spacing depends on the frequency of vibration.
- fracture toughness
fracture toughness
Critical value (KIC) of stress intensity. A material property.
- grooving
grooving
Machining grooves and shallow channels. Example: grooving ball-bearing raceways. Typically performed by tools that are capable of light cuts at high feed rates. Imparts high-quality finish.
- parting
parting
When used in lathe or screw-machine operations, this process separates a completed part from chuck-held or collet-fed stock by means of a very narrow, flat-end cutting, or parting, tool.
- profiling
profiling
Machining vertical edges of workpieces having irregular contours; normally performed with an endmill in a vertical spindle on a milling machine or with a profiler, following a pattern. See mill, milling machine.
- superalloys
superalloys
Tough, difficult-to-machine alloys; includes Hastelloy, Inconel and Monel. Many are nickel-base metals.
- toolholder
toolholder
Secures a cutting tool during a machining operation. Basic types include block, cartridge, chuck, collet, fixed, modular, quick-change and rotating.
- turning
turning
Workpiece is held in a chuck, mounted on a face plate or secured between centers and rotated while a cutting tool, normally a single-point tool, is fed into it along its periphery or across its end or face. Takes the form of straight turning (cutting along the periphery of the workpiece); taper turning (creating a taper); step turning (turning different-size diameters on the same work); chamfering (beveling an edge or shoulder); facing (cutting on an end); turning threads (usually external but can be internal); roughing (high-volume metal removal); and finishing (final light cuts). Performed on lathes, turning centers, chucking machines, automatic screw machines and similar machines.
- wear resistance
wear resistance
Ability of the tool to withstand stresses that cause it to wear during cutting; an attribute linked to alloy composition, base material, thermal conditions, type of tooling and operation and other variables.