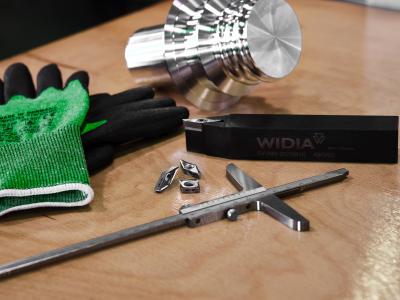
WIDIA has added an AL Geometry to its ISO Turning portfolio, strengthening its broad offering of affordable tooling solutions for small to medium sized machine shops, machining aluminum and non-ferrous materials. The AL Geometry insert is offered in two grades for increased machining versatility: an uncoated microfine carbide WU10HT grade and the PVD AlTiN coated grade, WU05PT. Each grade is available in all popular styles, including C, D, R, T, and V inserts to increase customer tooling options.
In addition to enhanced product versatility from multiple grade and style offerings, the AL Geometry insert offers additional benefits. A highly polished rake face improves chip flow, resulting in shorter set up times due to less manual retrieval of chips following each cut. The periphery ground insert also features a sharper cutting edge to increase overall tooling precision and reduce cutting forces. Reliable tooling performances means customers can dedicate more time to machining and less time to post-machining deburring operations because of the reduction in built-up edge.
“The AL Geometry portfolio offers tooling versatility when machining different components and workpieces, while also providing more precise and reliable machining performance,” said Anil Kumar, WIDIA Global Turning Portfolio Manager. “By focusing on both tooling performance and value, we’re helping our customers maximize their return on our products.”
Versatile, reliable, and cost-effective – the AL Geometry is the universal solution for customers seeking lower cutting forces, extended tool life, and greater tooling productivity when machining a variety of non-ferrous workpiece materials, particularly aluminum. Orders for new AL inserts and other WIDIA metal cutting tooling can be placed through any WIDIA authorized distribution partner.
Contact Details
Related Glossary Terms
- built-up edge ( BUE)
built-up edge ( BUE)
1. Permanently damaging a metal by heating to cause either incipient melting or intergranular oxidation. 2. In grinding, getting the workpiece hot enough to cause discoloration or to change the microstructure by tempering or hardening.
- physical vapor deposition ( PVD)
physical vapor deposition ( PVD)
Tool-coating process performed at low temperature (500° C), compared to chemical vapor deposition (1,000° C). Employs electric field to generate necessary heat for depositing coating on a tool’s surface. See CVD, chemical vapor deposition.
- rake
rake
Angle of inclination between the face of the cutting tool and the workpiece. If the face of the tool lies in a plane through the axis of the workpiece, the tool is said to have a neutral, or zero, rake. If the inclination of the tool face makes the cutting edge more acute than when the rake angle is zero, the rake is positive. If the inclination of the tool face makes the cutting edge less acute or more blunt than when the rake angle is zero, the rake is negative.
- turning
turning
Workpiece is held in a chuck, mounted on a face plate or secured between centers and rotated while a cutting tool, normally a single-point tool, is fed into it along its periphery or across its end or face. Takes the form of straight turning (cutting along the periphery of the workpiece); taper turning (creating a taper); step turning (turning different-size diameters on the same work); chamfering (beveling an edge or shoulder); facing (cutting on an end); turning threads (usually external but can be internal); roughing (high-volume metal removal); and finishing (final light cuts). Performed on lathes, turning centers, chucking machines, automatic screw machines and similar machines.