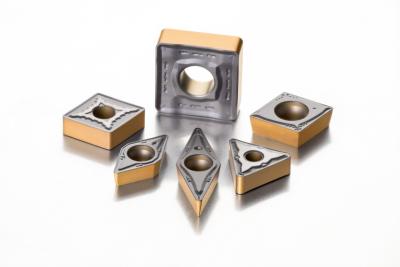
A new generation turning grade has been launched by Dormer Pramet offering one of the highest levels of productivity and versatility in the market today.
The Pramet T9415 is the most advanced MT-CVD grade launched by Dormer Pramet in almost ten years. This fourth-generation grade covers a broad application range, replacing the previous T9310 and T9315. In addition, it also partly overlaps with grade T9325, giving T9415 one of the widest range of applications in steel turning.
With a 30% thicker coating than the previous generation, the Pramet T9415 significantly improves tool durability by increasing resistance to wear and offers higher productivity by allowing for higher cutting speeds. Several testing users of the new grade have reported that their productivity has doubled while machining carbon and structural steels.
Additionally, a new post-treatment process improves toughness and stability of the cutting edge resulting in improved reliability in interrupted cuts and unstable conditions and is still suitable for high cutting speeds.
The insert seating area has been ground to improve stability and enhance heat transfer away from the cutting edge. This further helps to improve tool life, reducing the plastic wear on the cutting zones. Also, a gold TiN coating allows operators to better detect wear along the flank of the inserts.
Using the latest technologies, the Pramet T9415 inserts have optimized cutting-edge geometry which reduces cutting forces and enhances performance. Along with saving energy, the inserts themselves are manufactured using the latest production technologies and raw materials which support a more sustainable and environmentally friendly offer.
Contact Details
Related Glossary Terms
- titanium nitride ( TiN)
titanium nitride ( TiN)
Added to titanium-carbide tooling to permit machining of hard metals at high speeds. Also used as a tool coating. See coated tools.
- turning
turning
Workpiece is held in a chuck, mounted on a face plate or secured between centers and rotated while a cutting tool, normally a single-point tool, is fed into it along its periphery or across its end or face. Takes the form of straight turning (cutting along the periphery of the workpiece); taper turning (creating a taper); step turning (turning different-size diameters on the same work); chamfering (beveling an edge or shoulder); facing (cutting on an end); turning threads (usually external but can be internal); roughing (high-volume metal removal); and finishing (final light cuts). Performed on lathes, turning centers, chucking machines, automatic screw machines and similar machines.