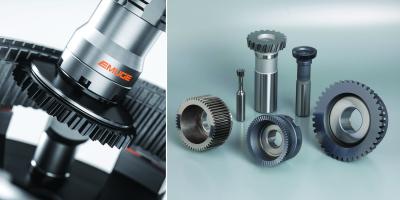
EMUGE-FRANKEN USA, a leading manufacturer of high-performance taps, thread mills, end mills, drills, and other rotary tools, offers gear manufacturers a single source for a full range of Skiving Tool Solutions including wheels for internal and external gears as bell-type or shank tool variants in the module sizes m 0.4 to m 5, as well as tool and workpiece clamping solutions. EMUGE-FRANKEN produces high-precision skiving tools on state-of-the-art tool grinding machines with appropriate grinding software. A measurement report and corresponding technology data are supplied with every delivery of skiving tools. Application specialists are available to assist with the initial use of the tools, and tool repair is also offered.
Skiving tools can be used in a variety of gear applications including the production of ring gears, shafts with internal and external splines and splined shaft profiles. EMUGE-FRANKEN Skiving Tools have no restrictions regarding the material to be machined and are highly suitable for the soft machining of internal and external gears, as well as hard machining. The skiving tools can be used on turning/ milling centers with B or A axes (swivel axes).
The EMUGE-FRANKEN clamping division specializes in providing highly accurate, almost maintenance-free customized solutions for applications ranging from low volume job shops to high volume automotive production environments. EMUGE-FRANKEN designs and develops optimal, often complex clamping solutions by working closely with its customers to learn about the unique application challenges and production environments.
Contact Details
Related Glossary Terms
- centers
centers
Cone-shaped pins that support a workpiece by one or two ends during machining. The centers fit into holes drilled in the workpiece ends. Centers that turn with the workpiece are called “live” centers; those that do not are called “dead” centers.
- gang cutting ( milling)
gang cutting ( milling)
Machining with several cutters mounted on a single arbor, generally for simultaneous cutting.
- grinding
grinding
Machining operation in which material is removed from the workpiece by a powered abrasive wheel, stone, belt, paste, sheet, compound, slurry, etc. Takes various forms: surface grinding (creates flat and/or squared surfaces); cylindrical grinding (for external cylindrical and tapered shapes, fillets, undercuts, etc.); centerless grinding; chamfering; thread and form grinding; tool and cutter grinding; offhand grinding; lapping and polishing (grinding with extremely fine grits to create ultrasmooth surfaces); honing; and disc grinding.
- milling
milling
Machining operation in which metal or other material is removed by applying power to a rotating cutter. In vertical milling, the cutting tool is mounted vertically on the spindle. In horizontal milling, the cutting tool is mounted horizontally, either directly on the spindle or on an arbor. Horizontal milling is further broken down into conventional milling, where the cutter rotates opposite the direction of feed, or “up” into the workpiece; and climb milling, where the cutter rotates in the direction of feed, or “down” into the workpiece. Milling operations include plane or surface milling, endmilling, facemilling, angle milling, form milling and profiling.
- shank
shank
Main body of a tool; the portion of a drill or similar end-held tool that fits into a collet, chuck or similar mounting device.