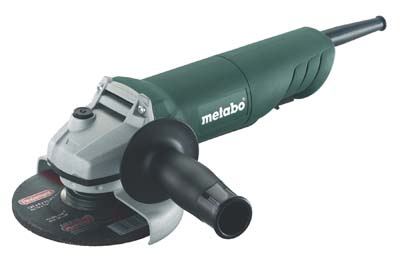
Metabo Corp. has introduced the new WP780 4 ½" angle grinder with a non-locking paddle switch. The WP780's "Deadman" function increases user safety by turning the grinder off automatically when its trigger is released or the tool is dropped.
Built to withstand rugged operating conditions including edge grinding, deburring, weld grinding, metal removal and tile cutting, the WP780 features a robust, 7.2 A motor with 780 watts of power, 14 inch-lbs of torque and a no-load speed of 11,000 rpm.
Weighing just 4.7 pounds, this lightweight grinder is reportedly ideal for overhead applications or ones that require the operator to reach. Its slim motor housing design and ergonomic 15 degree offset side handle make this grinder more comfortable to use than other grinders on the market. The WP780 includes a non-locking paddle switch and auto-stop carbon brushes.
Additionally, the WP780 includes a burst-proof wheel guard meeting the latest international standards. The new grinder comes standard with an inner flange, face spanner and outer nut. Optional equipment for the WP780 includes a Type 1 cut-off wheel guard and carrying case, as well as Metabo's wide range of abrasives. The WP780 is also covered by Metabo's XXL warranty This free warranty extends the normal one year power tool warranty to three years.
Contact Details
Related Glossary Terms
- grinding
grinding
Machining operation in which material is removed from the workpiece by a powered abrasive wheel, stone, belt, paste, sheet, compound, slurry, etc. Takes various forms: surface grinding (creates flat and/or squared surfaces); cylindrical grinding (for external cylindrical and tapered shapes, fillets, undercuts, etc.); centerless grinding; chamfering; thread and form grinding; tool and cutter grinding; offhand grinding; lapping and polishing (grinding with extremely fine grits to create ultrasmooth surfaces); honing; and disc grinding.
- turning
turning
Workpiece is held in a chuck, mounted on a face plate or secured between centers and rotated while a cutting tool, normally a single-point tool, is fed into it along its periphery or across its end or face. Takes the form of straight turning (cutting along the periphery of the workpiece); taper turning (creating a taper); step turning (turning different-size diameters on the same work); chamfering (beveling an edge or shoulder); facing (cutting on an end); turning threads (usually external but can be internal); roughing (high-volume metal removal); and finishing (final light cuts). Performed on lathes, turning centers, chucking machines, automatic screw machines and similar machines.