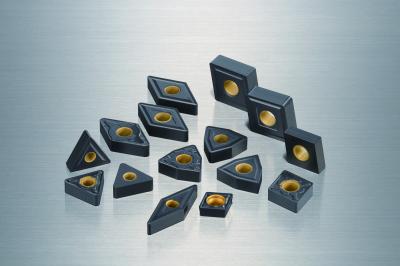
New from Sumitomo Electric Carbide Inc., AC4010K and AC4015K series turning grades for cast iron feature recently developed technologies that result in a long and stable tool life. Consisting of a smooth cutting edge treatment, the AC4000K series’ use of high adhesion technology drastically improves peeling resistance, according to the company. In addition, crystal orientation control technology provides double the wear resistance during high-speed machining compared with conventional products. The residual stress control technology of the AC4000K series further contributes to wear resistance.
Recommended for the precision cutting of gray cast iron, the extra-thick coating of the AC4010K grade allows for ultrahigh-speed machining (vc = 2,300 sfm). Its special surface treatment provides more than twice the compressive stress and 2 times the chipping resistance compared with conventional products.
The range of applications for the AC4010K grade includes cast iron brake discs and flywheels and ductile iron gear cases. Chipbreaker selection includes the EGU for low rigidity work, the ENZ for general finishing, the EGZ for extra cutting edge strength and the EME for strong and sharp high-feed cutting.
Contact Details
Related Glossary Terms
- chipbreaker
chipbreaker
Groove or other tool geometry that breaks chips into small fragments as they come off the workpiece. Designed to prevent chips from becoming so long that they are difficult to control, catch in turning parts and cause safety problems.
- residual stress
residual stress
Stress present in a body that is free of external forces or thermal gradients.
- turning
turning
Workpiece is held in a chuck, mounted on a face plate or secured between centers and rotated while a cutting tool, normally a single-point tool, is fed into it along its periphery or across its end or face. Takes the form of straight turning (cutting along the periphery of the workpiece); taper turning (creating a taper); step turning (turning different-size diameters on the same work); chamfering (beveling an edge or shoulder); facing (cutting on an end); turning threads (usually external but can be internal); roughing (high-volume metal removal); and finishing (final light cuts). Performed on lathes, turning centers, chucking machines, automatic screw machines and similar machines.
- wear resistance
wear resistance
Ability of the tool to withstand stresses that cause it to wear during cutting; an attribute linked to alloy composition, base material, thermal conditions, type of tooling and operation and other variables.