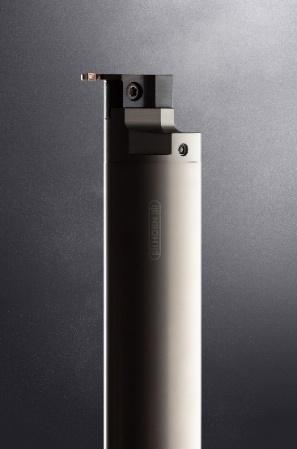
Long tool overhangs can cause a turning tool to oscillate when boring internal geometries. In addition to the resulting chatter marks on the surface, these vibrations also lead to a significant reduction in tool life. For unfavourable length/diameter ratios, the experienced machinist relies on vibration-damping boring bars, which enable low-vibration machining but which can still vibrate during certain machining operations. Paul Horn GmbH has addressed this problem and is presenting a boring bar at EMO in Hannover that can be adjusted to the vibration amplitudes that occur. Precise adjustment of the damping element in the boring bar enables a vibration-free grooving process. This results in better surface quality without chatter marks and a significant increase in tool life.
The exact adjustment of the damper, made of a carbide rod supported in O-rings, is made from the outside via an adjustment screw. Adjustment is achieved by fine-tuning the pre-tension of the O-rings. This allows the boring bar to be precisely set according to the vibration occurring in each application. As standard, Horn offers the tools from stock in the length/diameter ratios 5 x diameter and 8 x diameter. Higher ratios are possible as special tools. For the grooving processes, Horn offers the S224 double-edged grooving system. The Horn cassette system BK 224 ensures a stable interface between the boring bar and the inserts. To further increase process reliability, the boring bars are equipped with an internal coolant supply.
Contact Details
Related Glossary Terms
- boring
boring
Enlarging a hole that already has been drilled or cored. Generally, it is an operation of truing the previously drilled hole with a single-point, lathe-type tool. Boring is essentially internal turning, in that usually a single-point cutting tool forms the internal shape. Some tools are available with two cutting edges to balance cutting forces.
- boring bar
boring bar
Essentially a cantilever beam that holds one or more cutting tools in position during a boring operation. Can be held stationary and moved axially while the workpiece revolves around it, or revolved and moved axially while the workpiece is held stationary, or a combination of these actions. Installed on milling, drilling and boring machines, as well as lathes and machining centers.
- chatter
chatter
Condition of vibration involving the machine, workpiece and cutting tool. Once this condition arises, it is often self-sustaining until the problem is corrected. Chatter can be identified when lines or grooves appear at regular intervals in the workpiece. These lines or grooves are caused by the teeth of the cutter as they vibrate in and out of the workpiece and their spacing depends on the frequency of vibration.
- coolant
coolant
Fluid that reduces temperature buildup at the tool/workpiece interface during machining. Normally takes the form of a liquid such as soluble or chemical mixtures (semisynthetic, synthetic) but can be pressurized air or other gas. Because of water’s ability to absorb great quantities of heat, it is widely used as a coolant and vehicle for various cutting compounds, with the water-to-compound ratio varying with the machining task. See cutting fluid; semisynthetic cutting fluid; soluble-oil cutting fluid; synthetic cutting fluid.
- grooving
grooving
Machining grooves and shallow channels. Example: grooving ball-bearing raceways. Typically performed by tools that are capable of light cuts at high feed rates. Imparts high-quality finish.
- turning
turning
Workpiece is held in a chuck, mounted on a face plate or secured between centers and rotated while a cutting tool, normally a single-point tool, is fed into it along its periphery or across its end or face. Takes the form of straight turning (cutting along the periphery of the workpiece); taper turning (creating a taper); step turning (turning different-size diameters on the same work); chamfering (beveling an edge or shoulder); facing (cutting on an end); turning threads (usually external but can be internal); roughing (high-volume metal removal); and finishing (final light cuts). Performed on lathes, turning centers, chucking machines, automatic screw machines and similar machines.