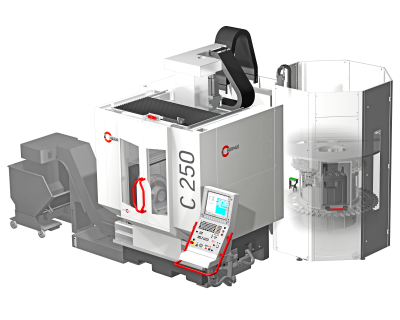
Hermle has introduced the C 250 as a complement to its existing C 400 unit (introduced in 2012), and offers yet another affordable way for customers to enter the 5-axis category while still delivering the precision required at the most demanding level of machining.
“This series offers the same design and precision 5-axis machining as our double-digit models, (C 12, C 22, C 42, C 52 and C 62), the only difference is the equipment variance and the price,” said Manuel Merkt, the company's vice president of operations. “This product line expansion provides an opportunity for Hermle to grow alongside our customers as they discover the next level of precision machining.”
“For some manufacturers, initial entry into this space can be intimidating and there is a learning curve, but the benefits of stepping up to 5-axis are tremendous. We help our customers achieve optimized results through comprehensive process consulting and project management. Our commitment to provide training and ongoing support is unparalleled in the industry,” said Vice President of Sales & Engineering Gunther Schnitzer. “Once they understand the technology, stunning level of precision, and overall efficiency that the C 250 and C 400 offer, there will be no looking back.”
The C 250 shares the C 400’s modified gantry design and mineral-cast machine bed. The high precision machining of workpieces weighing up to 300kg is possible on the NC swiveling rotary table of the 5-axis version.
The traverse path inside the working area is 600 x 550 x 450 mm for a vertical table clearance of 550 mm and a 688 mm door opening, creating optimal conditions for safe and simple crane loading.
To enhance its range of application, Hermle offers additional features for customized and cost-efficient utilization of the C 250 such as additional magazines, various cooling and chip systems, extractors, tool breakage monitoring/measuring and touch probes.
The C 250 provides an integrated tool magazine for 30 tools with the option to incorporate two additional magazines with 50 or 88 additional pockets. The control panel of the C250 is also pivotable from the working area to the tool loading point, thus allowing the operator to directly enter tool data information into the tool table control.
The C 250 comes standard with the Heidenhain TNC 640 and offers the entire scope of programming features provided by this proven high-end control unit. The control panel has a full-color 19” TFT flat-panel monitor and can be optionally equipped with an ergonomically designed control panel for greater operator comfort. A Hermle integrated control unit provides the operator with optimum support for complex milling tasks and the HIMS technology (Hermle
Information-Monitoring Software) is also standard with C 250 along with the Maintenance-Diagnostic System to facilitate efficient diagnostics and status-oriented maintenance in the unlikely event of malfunctioning.
Contact Details
Related Glossary Terms
- clearance
clearance
Space provided behind a tool’s land or relief to prevent rubbing and subsequent premature deterioration of the tool. See land; relief.
- gang cutting ( milling)
gang cutting ( milling)
Machining with several cutters mounted on a single arbor, generally for simultaneous cutting.
- milling
milling
Machining operation in which metal or other material is removed by applying power to a rotating cutter. In vertical milling, the cutting tool is mounted vertically on the spindle. In horizontal milling, the cutting tool is mounted horizontally, either directly on the spindle or on an arbor. Horizontal milling is further broken down into conventional milling, where the cutter rotates opposite the direction of feed, or “up” into the workpiece; and climb milling, where the cutter rotates in the direction of feed, or “down” into the workpiece. Milling operations include plane or surface milling, endmilling, facemilling, angle milling, form milling and profiling.
- numerical control ( NC)
numerical control ( NC)
Any controlled equipment that allows an operator to program its movement by entering a series of coded numbers and symbols. See CNC, computer numerical control; DNC, direct numerical control.
- precision machining ( precision measurement)
precision machining ( precision measurement)
Machining and measuring to exacting standards. Four basic considerations are: dimensions, or geometrical characteristics such as lengths, angles and diameters of which the sizes are numerically specified; limits, or the maximum and minimum sizes permissible for a specified dimension; tolerances, or the total permissible variations in size; and allowances, or the prescribed differences in dimensions between mating parts.