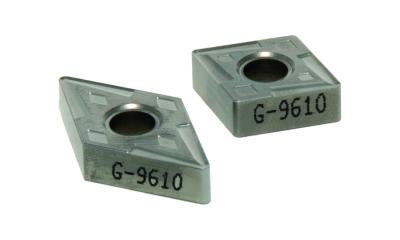
Greenleaf Corporation recently introduced carbide insert grade G-9610. This grade delivers a 25% increase in material removal rate and up to 100% increase in tool life versus the competition when machining titanium. G-9610 is a great addition to the Greenleaf portfolio.
Utilizing an innovative PVD coating combined with a proprietary sub-micron substrate, G-9610 provides added productivity for turning titanium-based alloys. The smooth and lubricious coating is wear-resistant and chemically-stable, which helps to protect the heat-resistant substrate and allows for higher speeds and extended tool life in continuous cuts. Other key attributes of G-9610 include:
-
High resistance to built-up edge (BUE), chemical wear, abrasive wear, and loss of hardness at high temperatures
-
Best applied at higher speeds and moderate feed rates
- Retains a sharp edge longer, relieving cutting forces and excessive heat
“This is a breakthrough technology for machining one of the most difficult materials – titanium,” says Bernie McConnell, Executive Vice President - Commercial at Greenleaf Corporation. “We are proud of our R&D team for again raising the bar and delivering a new titanium turning grade that offers increased value and productivity to our customers.”
Contact Details
Related Glossary Terms
- abrasive
abrasive
Substance used for grinding, honing, lapping, superfinishing and polishing. Examples include garnet, emery, corundum, silicon carbide, cubic boron nitride and diamond in various grit sizes.
- alloys
alloys
Substances having metallic properties and being composed of two or more chemical elements of which at least one is a metal.
- built-up edge ( BUE)
built-up edge ( BUE)
1. Permanently damaging a metal by heating to cause either incipient melting or intergranular oxidation. 2. In grinding, getting the workpiece hot enough to cause discoloration or to change the microstructure by tempering or hardening.
- feed
feed
Rate of change of position of the tool as a whole, relative to the workpiece while cutting.
- hardness
hardness
Hardness is a measure of the resistance of a material to surface indentation or abrasion. There is no absolute scale for hardness. In order to express hardness quantitatively, each type of test has its own scale, which defines hardness. Indentation hardness obtained through static methods is measured by Brinell, Rockwell, Vickers and Knoop tests. Hardness without indentation is measured by a dynamic method, known as the Scleroscope test.
- physical vapor deposition ( PVD)
physical vapor deposition ( PVD)
Tool-coating process performed at low temperature (500° C), compared to chemical vapor deposition (1,000° C). Employs electric field to generate necessary heat for depositing coating on a tool’s surface. See CVD, chemical vapor deposition.
- turning
turning
Workpiece is held in a chuck, mounted on a face plate or secured between centers and rotated while a cutting tool, normally a single-point tool, is fed into it along its periphery or across its end or face. Takes the form of straight turning (cutting along the periphery of the workpiece); taper turning (creating a taper); step turning (turning different-size diameters on the same work); chamfering (beveling an edge or shoulder); facing (cutting on an end); turning threads (usually external but can be internal); roughing (high-volume metal removal); and finishing (final light cuts). Performed on lathes, turning centers, chucking machines, automatic screw machines and similar machines.