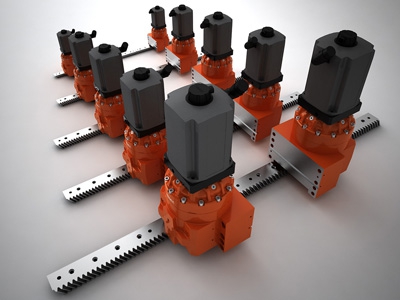
TCD (Total Cost of Design) and TCM (Total Cost of Manufacturing) are essential factors in maintaining a leading position in high-demand and competitive machine-tool markets worldwide. With one eye on the costs and the other on performance level, most of the machine-tool leaders have switched to the cubic concept, invented and developed by REDEX to enhance axis-drive global solutions.
Cubic concept entails that the machine frame on which the axis drives (mostly with Rack and Pinion planetary reducers inside) are fitted is no longer part of the machine but part of the drive itself. The cubic concept design offers numerous advantages, such as eliminating the need to design and integrate high-precision fixation extensions to the main machine frame. This key benefit greatly simplifies the design, saving many hours of stiffness simulation on sophisticated 3D CAD software and even more on real test proof campaigns. The implementation process is also streamlined, with only the need for very simple machining shapes for the fixation interfaces. This innovative advantage increases global savings on TCD and TCM by 15 to 20 percent, which is in stark contrast with other conventional solutions.
The core component of REDEX' axis drives is a very low backlash/very high stiffness planetary reducer, fully embedded in its own cubic frame and ready to be fitted to the machine mainframe exactly as if it would be a part of the frame itself.
Now available in the 5 standard universal sizes, KRPXng is a compact single drive, specially designed for the easy construction of 100 percent backlash-free axis drive systems (becoming a dual drive when used together with an electric preload). The latest design offers a significant implementation advantage with the pinion height not higher than 75.9 to 135mm.
Also available in the 5 standard universal sizes, DRPng is a DualDrive developed solution which combines two planetary reducers inside the same compact and ultra-high stiffness cubic housing unit. Cubic design of the DRP series even allows 100 percent backlash cancellation through a cost effective mechanical preload arrangement and greatly simplifies the setting-up process when an electric preload system is utilized.
Each machine subassembly and component must keep the global stiffness at the same level as the main frame, to avoid deterioration of global dynamic performances. The substantial stiffness of DRP and KRPX series is a result of the patented REDEX integral output pinion design with oversized output bearing. The output pinions are machined to the same diameter as the shafts, giving the optimal balance between transmissible torque and rigidity at the rack. The output bearing consists of two preloaded and substantially oversized angular contact roller bearings. This construction enables the bearing to support the pinion as close as possible to the force, as only the thickness of the fastening nut separates the pinion from the output bearing. This design considerably reduces radial bending, which is responsible for 60 percent of overall distortion that is still poorly managed by existing systems.
The housings structures have been optimised with FEM analysis methods to avoid deflection during acceleration. The fixation is made to ensure a still connection with the machine frame. This smart system has been designed to eliminate the risk of mounting system deflection.
The result is an increased dynamic working range, leading to the ability to displace heavier loads at higher speeds. Its performance in terms of stiffness combined with its low inertia enable higher accelerations (up to 25 m/s2). Consequently, the natural frequencies of the axis drive systems, in which the new series are embedded, are significantly improved.
After turning their latest R&D achievements into gear quality standard, REDEX engineers took another step forward, introducing a new gear finishing technology to the machine tool industry. This new technology, HQ-GF, ensures high-reversibility, significant noise reduction, and above all, a decrease of over 15 percent of power losses1. Thousands of kWh are saved in a machine's lifetime.
Contact Details
Related Glossary Terms
- backlash
backlash
Reaction in dynamic motion systems where potential energy that was created while the object was in motion is released when the object stops. Release of this potential energy or inertia causes the device to quickly snap backward relative to the last direction of motion. Backlash can cause a system’s final resting position to be different from what was intended and from where the control system intended to stop the device.
- computer-aided design ( CAD)
computer-aided design ( CAD)
Product-design functions performed with the help of computers and special software.
- stiffness
stiffness
1. Ability of a material or part to resist elastic deflection. 2. The rate of stress with respect to strain; the greater the stress required to produce a given strain, the stiffer the material is said to be. See dynamic stiffness; static stiffness.
- turning
turning
Workpiece is held in a chuck, mounted on a face plate or secured between centers and rotated while a cutting tool, normally a single-point tool, is fed into it along its periphery or across its end or face. Takes the form of straight turning (cutting along the periphery of the workpiece); taper turning (creating a taper); step turning (turning different-size diameters on the same work); chamfering (beveling an edge or shoulder); facing (cutting on an end); turning threads (usually external but can be internal); roughing (high-volume metal removal); and finishing (final light cuts). Performed on lathes, turning centers, chucking machines, automatic screw machines and similar machines.