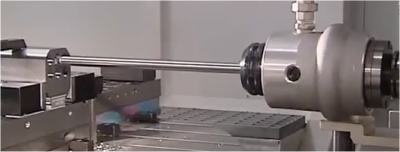
Investments in conventional deep-hole drilling machines can be very expensive. SOMEX, a member of the Suhner Group, offers custom deep-hole drilling solutions capable of drilling up to 12mm diameters and as deep as 100 times the diameter. These modules can be integrated directly into transfer machines, special-purpose machines or conventional machines such turning machines. The potential for cost savings is substantial.
In recent years, SOMEX has devoted considerable R&D time and capital resources to develop its deep-hole drilling technology, according to company sources.
In addition to standard MAX machining units, SOMEX can offer periphirel components. Thanks to its modular component concept, SOMEX can provide customized turnkey, small and economical deep-hole drilling machines.
SOMEX routinely conducts tests with actual tools and material to prove out the design and performance of its customized deep-hole drilling solutions. Tests are done at the factory, using specific production tools under real production conditions. SOMEX uses single cutting edge and carbide spiral drills up to 70 times the diameter. Using this approach, SOMEX can stand behind the design and performance and thus deliver practical and realistic results to its customers.
The deep-hole drilling process typically requires either a pilot-drill 1.5 times the diameter or a drill guide bushing, which is then followed by the deep-hole drilling process.
The unique SOMEX design concept combines the guide bushing with a chip basket, allowing both items to travel in unison. The movement of the guide bushing is air-driven, which helps to provide a much closer contact to the part while preventing the escape of the coolant medium. For longer deep-hole drilling applications, it may be necessary to integrate a support bushing to stabilize the deep hole drilling tool.
The degree of accuracy in a deep-hole drilling application measured in the deviation from the theoretical part center line is greatly enhanced by a slow part rotation in a counter-clockwise direction.
For deep-hole drilling applications above 18mm diameters, SOMEX has the option to equip its MAX machining units with drilling systems from BTA- or EJEKTOR lines. In these applications, the coolant and chip management is accomplished through the spindle center. The emulsion is collected at the backend of the spindle, filtered and pressurized to re-enter the coolant system. This solution is often used in high-volume precision parts manufacturing.
Contact Details
Related Glossary Terms
- bushing
bushing
Cylindrical sleeve, typically made from high-grade tool steel, inserted into a jig fixture to guide cutting tools. There are three main types: renewable, used in liners that in turn are installed in the jig; press-fit, installed directly in the jig for short production runs; and liner (or master), installed permanently in a jig to receive renewable bushing.
- coolant
coolant
Fluid that reduces temperature buildup at the tool/workpiece interface during machining. Normally takes the form of a liquid such as soluble or chemical mixtures (semisynthetic, synthetic) but can be pressurized air or other gas. Because of water’s ability to absorb great quantities of heat, it is widely used as a coolant and vehicle for various cutting compounds, with the water-to-compound ratio varying with the machining task. See cutting fluid; semisynthetic cutting fluid; soluble-oil cutting fluid; synthetic cutting fluid.
- drilling tool ( drill or drill bit)
drilling tool ( drill or drill bit)
End-cutting tool for drilling. Tool has shank, body and angled face with cutting edges that drill the hole. Drills range in size from “microdrills” a few thousandths of an inch in diameter up to spade drills, which may cut holes several inches in diameter. Drills may have tapered shanks with a driving tang and fit directly into a spindle or adapter, or they may have straight shanks and be chuck-mounted. The rake angle varies with the material drilled. Styles include twist drills, straight-flute drills, half-round and flat drills, oil-hole drills, indexable drills and specials.
- emulsion
emulsion
Suspension of one liquid in another, such as oil in water.
- turning
turning
Workpiece is held in a chuck, mounted on a face plate or secured between centers and rotated while a cutting tool, normally a single-point tool, is fed into it along its periphery or across its end or face. Takes the form of straight turning (cutting along the periphery of the workpiece); taper turning (creating a taper); step turning (turning different-size diameters on the same work); chamfering (beveling an edge or shoulder); facing (cutting on an end); turning threads (usually external but can be internal); roughing (high-volume metal removal); and finishing (final light cuts). Performed on lathes, turning centers, chucking machines, automatic screw machines and similar machines.