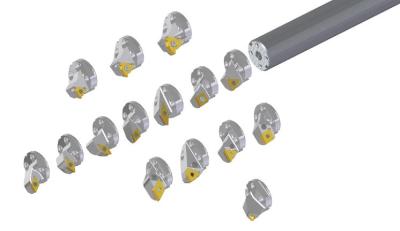
The best-damped bars in the world deserve the best possible cutter head!
Looking for the perfect cutter head for your damped bars? Look no further! We've got you covered with our top-notch cutter head collection.
We've taken the time to develop the most thought-through cutter heads on the market, addressing all your needs and more. With years of expertise, we ensure that our cutter heads hold the insert perfectly and distribute cutting fluid efficiently, giving you the results you expect.
Our cutter heads are designed to meet nearly all requirements, offering ISO standard cutter heads with the SL-Serration Lock interface for various applications like longitudinal turning, roughing, profile turning, threading, and more. We've got you covered from A to Z!
But wait, we've got something unique for you! Introducing our diamond burnishing cutter head, the first of its kind in the world! Get ready to achieve unmatched precision and quality in your machining projects.
We value your feedback and have incorporated it to ensure our cutter heads meet the highest standards. Our cutter heads feature a rigid clamping design, a flat surface for easy alignment, optimal toughness and impact strength, effective cooling, rust resistance, and more! We've left no stone unturned to make your machining experience seamless.
At MAQ, we strive to simplify machining for our customers. That's why we offer a wide range of accessories, including the best cutter heads, at a competitive price. Don't settle for less when you can have the best!
#Machining #CuttingTools #PrecisionEngineering #CutterHeads #QualityAssured
Our mission is to bring new technology to the workshops to make things better, faster, and easier. “Simplify Machining” in other words!
Contact Details
Related Glossary Terms
- burnishing
burnishing
Finishing method by means of compressing or cold-working the workpiece surface with carbide rollers called burnishing rolls or burnishers.
- cutting fluid
cutting fluid
Liquid used to improve workpiece machinability, enhance tool life, flush out chips and machining debris, and cool the workpiece and tool. Three basic types are: straight oils; soluble oils, which emulsify in water; and synthetic fluids, which are water-based chemical solutions having no oil. See coolant; semisynthetic cutting fluid; soluble-oil cutting fluid; synthetic cutting fluid.
- flat ( screw flat)
flat ( screw flat)
Flat surface machined into the shank of a cutting tool for enhanced holding of the tool.
- threading
threading
Process of both external (e.g., thread milling) and internal (e.g., tapping, thread milling) cutting, turning and rolling of threads into particular material. Standardized specifications are available to determine the desired results of the threading process. Numerous thread-series designations are written for specific applications. Threading often is performed on a lathe. Specifications such as thread height are critical in determining the strength of the threads. The material used is taken into consideration in determining the expected results of any particular application for that threaded piece. In external threading, a calculated depth is required as well as a particular angle to the cut. To perform internal threading, the exact diameter to bore the hole is critical before threading. The threads are distinguished from one another by the amount of tolerance and/or allowance that is specified. See turning.
- turning
turning
Workpiece is held in a chuck, mounted on a face plate or secured between centers and rotated while a cutting tool, normally a single-point tool, is fed into it along its periphery or across its end or face. Takes the form of straight turning (cutting along the periphery of the workpiece); taper turning (creating a taper); step turning (turning different-size diameters on the same work); chamfering (beveling an edge or shoulder); facing (cutting on an end); turning threads (usually external but can be internal); roughing (high-volume metal removal); and finishing (final light cuts). Performed on lathes, turning centers, chucking machines, automatic screw machines and similar machines.