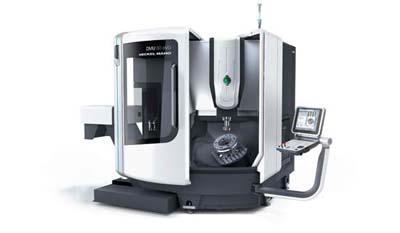
The DMU 60 eVo from DMG/Mori Seiki USA is the newest model in its successful eVo Series, having already sold more than 3,000 units throughout the world. In recent years, there has been growing demand for manufacturing complex workpieces, particularly in the aircraft and medical equipment industries. The company has launched the DMU 60 eVo in order to meet this demand.
The distinctive features of the DMU 60 eVo include a revolutionary gantry design for highest rigidity and precision, improved swivel rotary table, space saving design and optional linear motor drive.
The DMU 60 eVo has a gantry construction in which the X and Y axes are placed in the upper part of the machine. This construction enables the machine to minimize spindle overhang and increase stability and rigidity, thereby maintaining high precision. Additionally, the optimally positioned Y-axis saddle and the rounded design for the front of the machine provide efficient setups and outstanding accessibility to the working area from two sides.
The eVo Series' proven swivel rotary table has been further strengthened. The 600 x 500mm swivel rotary table maintains the successful design concept, while doubling the loading capacity to 400 kg. Turning specifications with a C-axis rotational speed of 1,000 min-1 (FD specifications) are also available as an option.
A standard DMU 60 eVo uses a ball screw drive for the X and Y axes (rapid traverse rate: 50 m/min). The optional linear motor drive (rapid traverse rate: 80 m/min) is ideal for customers who need even greater efficiency. The linear motor drive offers high speed and high acceleration feed, and achieves superb positioning accuracy, with a positioning error only one-tenth of that of the ball screw drive. Additionally, the machine uses fewer consumable parts, which requires less maintenance.
With a footprint of 6.1 sq. m, the DMU 60 eVo is reportedly the most compact machine in its class. And, due to the machine's unique construction, the footprint stays almost the same, regardless of the size of the tool magazine.
Contact Details
Related Glossary Terms
- feed
feed
Rate of change of position of the tool as a whole, relative to the workpiece while cutting.
- linear motor
linear motor
Functionally the same as a rotary motor in a machine tool, a linear motor can be thought of as a standard permanent-magnet, rotary-style motor slit axially to the center and then peeled back and laid flat. The major advantage of using a linear motor to drive the axis motion is that it eliminates the inefficiency and mechanical variance caused by the ballscrew assembly system used in most CNC machines.
- turning
turning
Workpiece is held in a chuck, mounted on a face plate or secured between centers and rotated while a cutting tool, normally a single-point tool, is fed into it along its periphery or across its end or face. Takes the form of straight turning (cutting along the periphery of the workpiece); taper turning (creating a taper); step turning (turning different-size diameters on the same work); chamfering (beveling an edge or shoulder); facing (cutting on an end); turning threads (usually external but can be internal); roughing (high-volume metal removal); and finishing (final light cuts). Performed on lathes, turning centers, chucking machines, automatic screw machines and similar machines.