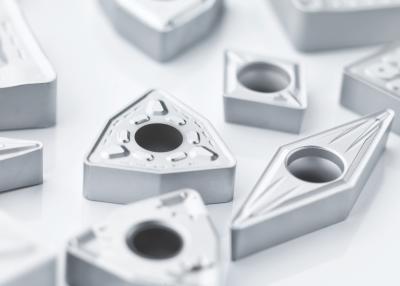
Seco Tools has expanded its family of Duratomictechnology-based TP grades to include TP3501, a grade that reportedly provides optimal application security. The new grade is ideal for steel turning applications that involve numerous interrupted cuts, less stable machines, short time in cut or weak setups due to part size or shape.
TP3501 joins TP2501, TP1501 and TP0501 to complete the grade offering for steel turning and features Seco’s latest Duratomic technology-based coatings for reliable performance in specific cutting materials and applications. Introduced by Seco in 2007 as the industry’s first textured, a-based Al2O3 coating, Duratomic technology manipulates
coating components at an atomic level to achieve improved mechanical and thermal properties. The technology enhances performance by attaining the elusive balance of toughness and hardness.
The new TP grade also incorporates Seco’s EDGE INTELLIGENCE concept – an integration of extensive high-performance insert experience and knowledge that features Chrome Used-Edge Detection, which allows a user to instantly identify when an edge has been used, thus making every edge count and reducing potential waste. The comprehensive range for TP3501 includes nearly 400 inserts in a variety of available geometries and chipbreakers, including the broadly applicable M6.
Contact Details
Related Glossary Terms
- hardness
hardness
Hardness is a measure of the resistance of a material to surface indentation or abrasion. There is no absolute scale for hardness. In order to express hardness quantitatively, each type of test has its own scale, which defines hardness. Indentation hardness obtained through static methods is measured by Brinell, Rockwell, Vickers and Knoop tests. Hardness without indentation is measured by a dynamic method, known as the Scleroscope test.
- turning
turning
Workpiece is held in a chuck, mounted on a face plate or secured between centers and rotated while a cutting tool, normally a single-point tool, is fed into it along its periphery or across its end or face. Takes the form of straight turning (cutting along the periphery of the workpiece); taper turning (creating a taper); step turning (turning different-size diameters on the same work); chamfering (beveling an edge or shoulder); facing (cutting on an end); turning threads (usually external but can be internal); roughing (high-volume metal removal); and finishing (final light cuts). Performed on lathes, turning centers, chucking machines, automatic screw machines and similar machines.