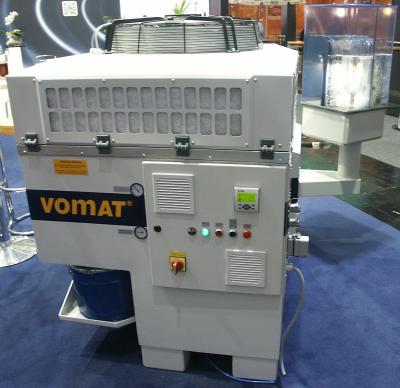
Optimally cleaned lubricants play a decisive role in tool grinding since chips, wheel abrasion and other particles can negatively impact the grinding process. Capable and energy-efficient filtration is becoming more and more important especially when considering todays’ tightly defined tolerances for tools and micro tools in particular. Excellent filtration can also save money by extending coolant life and reducing non-productive time which cut the costs of purchasing, storage, recycling and energy consumption.
Clean coolant in carbide and HSS tool grinding is important in creating a safe work environment and is partly responsible for the quality of the end product. VOMAT GmbH from Germany provides fine filtration systems that separate dirty and clean oil 100 percent with their full flow filtration process. The filter throughput and backwash cycles are automatically adjusted as needed. This extends the life of the filter elements and saves energy and costs.
Steffen Strobel, technical sales manager at VOMAT states: "Many filtration systems on the market filter permanently at full capacity, even if this is not necessary. In contrast, VOMAT systems adapt to the production process. For example, if grinding machines operate slowly, only the required amount of cooling lubricant is filtered."
Another example is when a VOMAT system filters coolant from several grinding machines. If some of grinders are not in operation, the filter capacity of the VOMAT machine automatically adapts to the production volume. At the same time less heat is transferred to the coolant which in turn reduces the need for cooling. This ultimately minimizes the energy expenditure.
With their full-flow filtration, VOMAT filtration systems permanently provide clean oil meeting NAS 7 quality (3-5 μm). The on-demand back-flushing system offers further benefits: the filter and machine components are less stressed and in turn the energy consumption is reduced. According to VOMAT, conventional systems operating in bypass mode do not produce any clean oil during the back-flushing cycle and, as a result, dirty oil will remain circulating in the system. On VOMAT filtration systems, the backwash cycles are controlled by the degree of filter cartridge contamination. Once those levels are reached, the back-flushing process begins by cleaning each filter cartridge individually. The filters which are not being back-flushed remain in service to ensure a continuous supply of clean oil. In the disposal unit, the back-flushed oil is separated from most of the sludge and conveyed into the dirty oil tank. As a result, VOMAT claims, the service life of each individual filter element increases significantly and the coolant can remain in the system for longer periods of time while saving energy at the same time.
Strobel said: "The decision to use an efficient and energy-efficient filtration system will affect the production costs directly. VOMAT has developed this innovative technology to optimally adapt to any production situation through on-demand filtering and back-flushing which automatically minimizes energy consumption. Altogether this can save a lot of production costs. "
Contact Details
Related Glossary Terms
- coolant
coolant
Fluid that reduces temperature buildup at the tool/workpiece interface during machining. Normally takes the form of a liquid such as soluble or chemical mixtures (semisynthetic, synthetic) but can be pressurized air or other gas. Because of water’s ability to absorb great quantities of heat, it is widely used as a coolant and vehicle for various cutting compounds, with the water-to-compound ratio varying with the machining task. See cutting fluid; semisynthetic cutting fluid; soluble-oil cutting fluid; synthetic cutting fluid.
- grinding
grinding
Machining operation in which material is removed from the workpiece by a powered abrasive wheel, stone, belt, paste, sheet, compound, slurry, etc. Takes various forms: surface grinding (creates flat and/or squared surfaces); cylindrical grinding (for external cylindrical and tapered shapes, fillets, undercuts, etc.); centerless grinding; chamfering; thread and form grinding; tool and cutter grinding; offhand grinding; lapping and polishing (grinding with extremely fine grits to create ultrasmooth surfaces); honing; and disc grinding.
- high-speed steels ( HSS)
high-speed steels ( HSS)
Available in two major types: tungsten high-speed steels (designated by letter T having tungsten as the principal alloying element) and molybdenum high-speed steels (designated by letter M having molybdenum as the principal alloying element). The type T high-speed steels containing cobalt have higher wear resistance and greater red (hot) hardness, withstanding cutting temperature up to 1,100º F (590º C). The type T steels are used to fabricate metalcutting tools (milling cutters, drills, reamers and taps), woodworking tools, various types of punches and dies, ball and roller bearings. The type M steels are used for cutting tools and various types of dies.