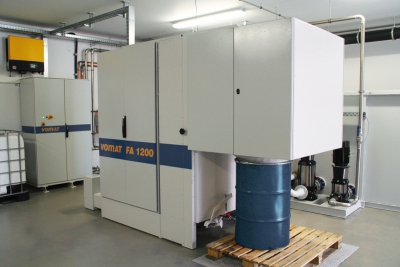
VOMAT says its full-flow filtration technology completely separates dirty oil from clean oil and allows for grinding with optimally cleaned cooling lubricants. VOMAT’s filtration systems clean the oil so efficiently that it’s useful life is much longer than if it were filtered with conventional filter systems still using paper filters or other expensive disposable filter media. A pleasant side effect is the low operating costs.
Coolants become contaminated during manufacture with chips, abrasion and other solid contaminants. If these contaminants are not constantly filtered out, metal coolants need to be changed more often and surface finish of the ground tool is often poor.
Michael Kramer, head of design at VOMAT, states: "No tool manufacturer can afford this nowadays. Cooling lubricants can only perform to their fullest potential when they are optimally cleaned. A major shortcoming of most conventional filter systems used in the carbide and HSS grinding industry is that they operate in bypass filtration mode. There, the grinding oil is filtered only partially, and a certain percentage of contaminated oil remains in the system and in the oil stream. In order to guarantee a long service life of the coolant, bypass filtration is not recommended nor is the use of expensive filtration aids such as perlite or cellulose. "
VOMAT’s fine filtration technology is based on the use of high-capacity, pre-coat filters in full-flow filtration. Dirty and clean oil are separated 100 percent and filtered to quality class NAS 7 (3-5 microns). The backwash process is initiated automatically depending on the contamination level. Each filter element is monitored individually and cleaned individually while the remaining filter elements guarantee a continuous clean oil supply up to the nominal filter capacity of the machine during the backwash cycle.
Kramer continues: "The filters are designed in such fashion that we use fewer filter elements compared to other systems. VOMAT filters are slightly larger than most conventional systems but at the same time more efficient.”
With VOMAT filters there are no ongoing operating costs as there are with short-lived disposable filter cartridges or paper band filters. Moreover, VOMAT equipment is designed to filter only when needed, which provides the tool maker with many economic benefits.
VOMAT systems adjust automatically to any given production load. For example, when grinding machines operate in a slower mode, only the required amount of cooling lubricant for this slower operating mode is filtered. If a VOMAT system is hooked up to two grinding machines but only one machine is operating then only half the amount of oil is processed by these intelligent systems. This means that only half of the normal amount energy is consumed and introduces less heat to the coolant therefore requiring a lot less cooling capacity. Less cooling translates into added energy savings.
VOMAT filtration systems come as compact standalone units on up to large scale industrial systems. By default, VOMAT FA series standalone models have a throughput capacity of 70 to 960 liters per minute. VOMAT systems can easily be adapted to user-specific needs with the help of a wide variety of add-on modules. Displays for the visualization of system performance, frequency-controlled machine supply pumps or internal and external pre-filters, as well as various styles of chiller systems are just some examples of the wide range of additional modules.
In addition to the FA-series standalone units, VOMAT provides plant-wide, customizable Central filter systems (ZFA). The ZFA series advantage is: They consist of separate modules that can be flexibly combined. VOMAT assembles the necessary components to match the customer’s requirements. Michael Kramer states: "In case production requirements or capacities change, the system can be expanded with appropriate prior planning. This allows for maximum performance in various stages of production and business growth - always optimally adapted to the individual needs of the user."
Contact Details
Related Glossary Terms
- bandsaw blade ( band)
bandsaw blade ( band)
Endless band, normally with serrated teeth, that serves as the cutting tool for cutoff or contour band machines.
- coolant
coolant
Fluid that reduces temperature buildup at the tool/workpiece interface during machining. Normally takes the form of a liquid such as soluble or chemical mixtures (semisynthetic, synthetic) but can be pressurized air or other gas. Because of water’s ability to absorb great quantities of heat, it is widely used as a coolant and vehicle for various cutting compounds, with the water-to-compound ratio varying with the machining task. See cutting fluid; semisynthetic cutting fluid; soluble-oil cutting fluid; synthetic cutting fluid.
- grinding
grinding
Machining operation in which material is removed from the workpiece by a powered abrasive wheel, stone, belt, paste, sheet, compound, slurry, etc. Takes various forms: surface grinding (creates flat and/or squared surfaces); cylindrical grinding (for external cylindrical and tapered shapes, fillets, undercuts, etc.); centerless grinding; chamfering; thread and form grinding; tool and cutter grinding; offhand grinding; lapping and polishing (grinding with extremely fine grits to create ultrasmooth surfaces); honing; and disc grinding.
- high-speed steels ( HSS)
high-speed steels ( HSS)
Available in two major types: tungsten high-speed steels (designated by letter T having tungsten as the principal alloying element) and molybdenum high-speed steels (designated by letter M having molybdenum as the principal alloying element). The type T high-speed steels containing cobalt have higher wear resistance and greater red (hot) hardness, withstanding cutting temperature up to 1,100º F (590º C). The type T steels are used to fabricate metalcutting tools (milling cutters, drills, reamers and taps), woodworking tools, various types of punches and dies, ball and roller bearings. The type M steels are used for cutting tools and various types of dies.