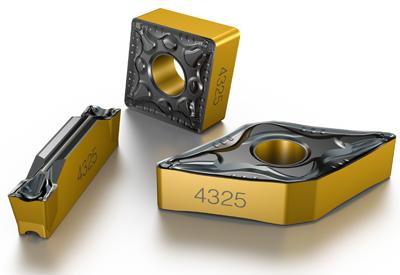
With new technological developments, emerging on the automotive horizon, manufacturers are faced with extremely high demands in terms of quality, security and productivity. The new Sandvik Coromant grades GC4315 and GC4325 with Inveio are designed to support the automotive industry with outstanding reliability and process security.
Transmission manufacturing is a large volume production with a low cost per part. Therefore, requirements such as high process security, short cycle times and consistent quality are critical for achieving faster lead times and lower production costs. Soft stage turning is performed before the case hardening process. Offering high wear resistance and excellent tool life, this is where the steel turning grades GC4315 and GC4325 are to show a marked step up in performance.
First choice grade for soft stage turning in stable conditions, GC4315, is designed for high-speed steel turning with a long and predictable tool life. Grade GC4325 is a tougher steel turning grade that manages interrupted cuts and uneven depths of cut at high speeds. Both grades enable high cutting data without sacrificing component quality. If the spindle speed limit prevents the full use of their capacity, maximum productivity can be achieved by applying higher feed rates. These two grades are excellent choices for outer-diameter turning, copying and profiling and guarantee predictable performance for secure transmission manufacturing.
Contact Details
Related Glossary Terms
- feed
feed
Rate of change of position of the tool as a whole, relative to the workpiece while cutting.
- hardening
hardening
Process of increasing the surface hardness of a part. It is accomplished by heating a piece of steel to a temperature within or above its critical range and then cooling (or quenching) it rapidly. In any heat-treatment operation, the rate of heating is important. Heat flows from the exterior to the interior of steel at a definite rate. If the steel is heated too quickly, the outside becomes hotter than the inside and the desired uniform structure cannot be obtained. If a piece is irregular in shape, a slow heating rate is essential to prevent warping and cracking. The heavier the section, the longer the heating time must be to achieve uniform results. Even after the correct temperature has been reached, the piece should be held at the temperature for a sufficient period of time to permit its thickest section to attain a uniform temperature. See workhardening.
- profiling
profiling
Machining vertical edges of workpieces having irregular contours; normally performed with an endmill in a vertical spindle on a milling machine or with a profiler, following a pattern. See mill, milling machine.
- turning
turning
Workpiece is held in a chuck, mounted on a face plate or secured between centers and rotated while a cutting tool, normally a single-point tool, is fed into it along its periphery or across its end or face. Takes the form of straight turning (cutting along the periphery of the workpiece); taper turning (creating a taper); step turning (turning different-size diameters on the same work); chamfering (beveling an edge or shoulder); facing (cutting on an end); turning threads (usually external but can be internal); roughing (high-volume metal removal); and finishing (final light cuts). Performed on lathes, turning centers, chucking machines, automatic screw machines and similar machines.
- wear resistance
wear resistance
Ability of the tool to withstand stresses that cause it to wear during cutting; an attribute linked to alloy composition, base material, thermal conditions, type of tooling and operation and other variables.