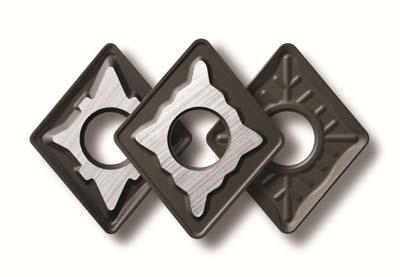
Seco Tools Inc. has announced the availability of TP0500, its newest turning grade to feature one of the company's wear-resistant Duratomic coatings. The new grade is suited to a variety of steel machining operations with stable cutting conditions and where a lot of heat is generated. Applications that can make significant gains using TP0500 include those requiring high metal-removal rates, such as the machining of large components for the power generation segment or for high-speed, high-productivity applications found in the automotive sector. Benefits of the new grade include increased speed capability--even with a long time in cut, fewer machine offsets, longer times between insert indexes and the ability to machine harder parts and to hold tighter tolerances. The wear-resistance of the TP0500 grade is due to its Duratomic coating in combination with a plastic-deformation resistant fine-grained substrate. Seco says its Duratomic coatings have proven to be about 15 percent tougher and 10 harder harder than traditional coatings. In tests run under identical conditions, an insert coated with the Duratomic process runs cooler compared to an identical insert coated with a conventional aluminum oxide coating. This means less crater wear, less deformation of the cutting edge and longer tool life. Grade TP0500 is offered in a complete range of chipbreaker geometries that includes negative inserts, positive inserts and high-feed wiper inserts.
Contact Details
Related Glossary Terms
- aluminum oxide
aluminum oxide
Aluminum oxide, also known as corundum, is used in grinding wheels. The chemical formula is Al2O3. Aluminum oxide is the base for ceramics, which are used in cutting tools for high-speed machining with light chip removal. Aluminum oxide is widely used as coating material applied to carbide substrates by chemical vapor deposition. Coated carbide inserts with Al2O3 layers withstand high cutting speeds, as well as abrasive and crater wear.
- chipbreaker
chipbreaker
Groove or other tool geometry that breaks chips into small fragments as they come off the workpiece. Designed to prevent chips from becoming so long that they are difficult to control, catch in turning parts and cause safety problems.
- turning
turning
Workpiece is held in a chuck, mounted on a face plate or secured between centers and rotated while a cutting tool, normally a single-point tool, is fed into it along its periphery or across its end or face. Takes the form of straight turning (cutting along the periphery of the workpiece); taper turning (creating a taper); step turning (turning different-size diameters on the same work); chamfering (beveling an edge or shoulder); facing (cutting on an end); turning threads (usually external but can be internal); roughing (high-volume metal removal); and finishing (final light cuts). Performed on lathes, turning centers, chucking machines, automatic screw machines and similar machines.
- wiper
wiper
Metal-removing edge on the face of a cutter that travels in a plane perpendicular to the axis. It is the edge that sweeps the machined surface. The flat should be as wide as the feed per revolution of the cutter. This allows any given insert to wipe the entire workpiece surface and impart a fine surface finish at a high feed rate.