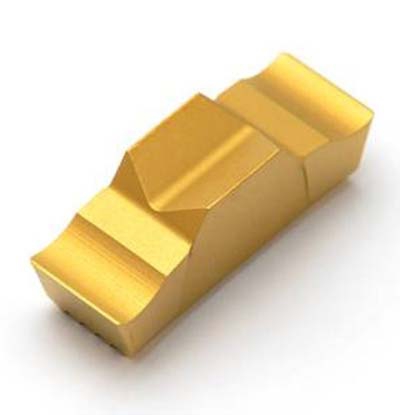
Seco Tools Inc. continues to enhance its Multi-Directional Turning (MDT) program, most recently announcing the GS (Grooving Sharp) and GG (Grooving Ground) chipbreakers for grooving steel, nonferrous alloys and superalloys. The chipbreakers feature a positive rake angle of 10 degrees with a sharp edge of 10-micron honing. The GS geometry features a sharp edge without any protection chamfer and is mainly intended for nonferrous alloys. The GG (pictured) chipbreaker, which has a protection chamfer from 0.1mm to 0.2mm, is aimed at superalloys, but can also be applied in some steel applications. Both chipbreakers reduce cutting tool pressure to increase productivity and are to be used as "problem solvers" in applications where light cutting is more important than chipbreaking capability, according to the company. Seco's MDT is a flexible system that uses a single toolholder and insert for turning, profiling and grooving in both axial and radial directions. The toolholder features a clamping action that reportedly provides a rigid and stable contact surface.
Contact Details
Related Glossary Terms
- alloys
alloys
Substances having metallic properties and being composed of two or more chemical elements of which at least one is a metal.
- chipbreaker
chipbreaker
Groove or other tool geometry that breaks chips into small fragments as they come off the workpiece. Designed to prevent chips from becoming so long that they are difficult to control, catch in turning parts and cause safety problems.
- grooving
grooving
Machining grooves and shallow channels. Example: grooving ball-bearing raceways. Typically performed by tools that are capable of light cuts at high feed rates. Imparts high-quality finish.
- profiling
profiling
Machining vertical edges of workpieces having irregular contours; normally performed with an endmill in a vertical spindle on a milling machine or with a profiler, following a pattern. See mill, milling machine.
- rake
rake
Angle of inclination between the face of the cutting tool and the workpiece. If the face of the tool lies in a plane through the axis of the workpiece, the tool is said to have a neutral, or zero, rake. If the inclination of the tool face makes the cutting edge more acute than when the rake angle is zero, the rake is positive. If the inclination of the tool face makes the cutting edge less acute or more blunt than when the rake angle is zero, the rake is negative.
- superalloys
superalloys
Tough, difficult-to-machine alloys; includes Hastelloy, Inconel and Monel. Many are nickel-base metals.
- toolholder
toolholder
Secures a cutting tool during a machining operation. Basic types include block, cartridge, chuck, collet, fixed, modular, quick-change and rotating.
- turning
turning
Workpiece is held in a chuck, mounted on a face plate or secured between centers and rotated while a cutting tool, normally a single-point tool, is fed into it along its periphery or across its end or face. Takes the form of straight turning (cutting along the periphery of the workpiece); taper turning (creating a taper); step turning (turning different-size diameters on the same work); chamfering (beveling an edge or shoulder); facing (cutting on an end); turning threads (usually external but can be internal); roughing (high-volume metal removal); and finishing (final light cuts). Performed on lathes, turning centers, chucking machines, automatic screw machines and similar machines.