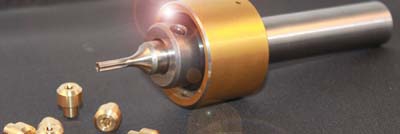
The rotary broach allows machinists to add internal hexagon, square and other forms to precision metal parts. The modern machine shop can benefit from the quick set-up and ease of use available in adjustment free broach holders. The GT Series broach holder from Polygon Solutions has been designed for this purpose, and often eliminates secondary operations.
The single pass broach is held on center in the holder at a one degree angle. Thus, the full force of the machine is directed to the cutting edge closest to the part. Since this is a turning operation, the cutting action will rotate to every edge, and as the tool is fed into the pilot hole the desired depth is achieved.
The GT Series rotary broach holder requires no centering, indicating or alignment procedures. The broaches are cut to a specified length. When fastened into the holder the broaches are designed to be on center with the pilot hole. A small amount of endplay insures that the broach will follow the chamfer of the hole.
When broaching a blind hole, it is possible that hydraulic pressure can build up due to air and fluid that may get trapped inside. Polygon Solution's rotary broaches and GT series broach holders include a pressure relief hole to eliminate hydraulic pressure. Air and fluid are pushed through the hole in the broach, and then can escape through the hole in the broach holder.
The GT Series rotary broach holder is available with two different spindles. One spindle accommodates 8mm shank broaches, and the other holds .500" shank broaches. Although the 8mm broaches may cost a little less, the .500" shank broaches are available in more sizes. Rotary broaching is ideal for forms within this size range.
The bearing configuration of the broach holder is designed to handle the loads associated with rotary broaching. The sealed design requires no maintenance or messy grease guns. Help with speed and feed rate is available from Polygon Solutions.
Rotary broaching will work on most machines with spindles, including lathes, mills, and machining centers. Different shank sizes to fit into your machine are available in metric and inch sizes.
Contact Details
Related Glossary Terms
- broach
broach
Tapered tool, with a series of teeth of increasing length, that is pushed or pulled into a workpiece, successively removing small amounts of metal to enlarge a hole, slot or other opening to final size.
- broaching
broaching
Operation in which a cutter progressively enlarges a slot or hole or shapes a workpiece exterior. Low teeth start the cut, intermediate teeth remove the majority of the material and high teeth finish the task. Broaching can be a one-step operation, as opposed to milling and slotting, which require repeated passes. Typically, however, broaching also involves multiple passes.
- centering
centering
1. Process of locating the center of a workpiece to be mounted on centers. 2. Process of mounting the workpiece concentric to the machine spindle. See centers.
- centers
centers
Cone-shaped pins that support a workpiece by one or two ends during machining. The centers fit into holes drilled in the workpiece ends. Centers that turn with the workpiece are called “live” centers; those that do not are called “dead” centers.
- feed
feed
Rate of change of position of the tool as a whole, relative to the workpiece while cutting.
- relief
relief
Space provided behind the cutting edges to prevent rubbing. Sometimes called primary relief. Secondary relief provides additional space behind primary relief. Relief on end teeth is axial relief; relief on side teeth is peripheral relief.
- shank
shank
Main body of a tool; the portion of a drill or similar end-held tool that fits into a collet, chuck or similar mounting device.
- turning
turning
Workpiece is held in a chuck, mounted on a face plate or secured between centers and rotated while a cutting tool, normally a single-point tool, is fed into it along its periphery or across its end or face. Takes the form of straight turning (cutting along the periphery of the workpiece); taper turning (creating a taper); step turning (turning different-size diameters on the same work); chamfering (beveling an edge or shoulder); facing (cutting on an end); turning threads (usually external but can be internal); roughing (high-volume metal removal); and finishing (final light cuts). Performed on lathes, turning centers, chucking machines, automatic screw machines and similar machines.