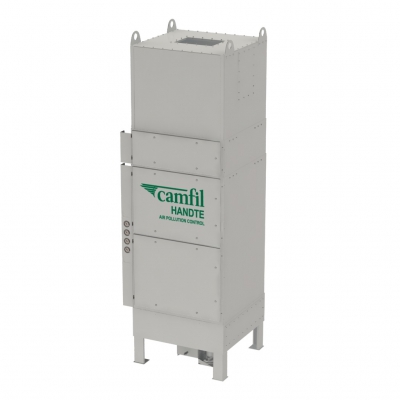
Collecting mist from lubricant oils used to cool machining processes is critical to protect workers' health and meet OSHA requirements. The Handte Oil Expert from Camfil APC helps facility operators reduce exhaust emissions to meet the current OSHA 5.0 mg/m3 exposure limit for oil mist. It also eliminates the ongoing housekeeping expenses required to remove oil from heating and cooling equipment, other machinery and workplace surfaces.
The Handte Oil Expert uses multiple-stage filtration and high-efficiency CoaPack filters to remove 99.97 percent of oil mist contaminant particles as small as 0.3 microns. All air must pass through a three-stage filtration process and out of a HEPA filter before returning to the workplace.
Filter gauges with "filter full" indicators monitor all filter stages to ensure easy and effective maintenance. In addition, filter changes don't require specialized tools or knowledge, and the closed filter cassettes eliminate worker exposure to the dirty filter media.
"Maintaining a safe working environment for operators of machine tools and other processes exposed to these fine aerosol mists is both an OSHA requirement and a workplace obligation for plant owners," said Graeme Bell, vice president of Camfil APC Americas. "The Handte Oil Expert helps manufacturers achieve both of these goals."
The Handte Oil Expert is ideal for applications that use straight/neat oil including turning, drilling, grinding and pressing. Its modular design enables it to be customized to suit a facility's current needs and future expansion. It also comes with a guarantee that the weld seams and collector will not leak coolant or oil.
Contact Details
Related Glossary Terms
- coolant
coolant
Fluid that reduces temperature buildup at the tool/workpiece interface during machining. Normally takes the form of a liquid such as soluble or chemical mixtures (semisynthetic, synthetic) but can be pressurized air or other gas. Because of water’s ability to absorb great quantities of heat, it is widely used as a coolant and vehicle for various cutting compounds, with the water-to-compound ratio varying with the machining task. See cutting fluid; semisynthetic cutting fluid; soluble-oil cutting fluid; synthetic cutting fluid.
- grinding
grinding
Machining operation in which material is removed from the workpiece by a powered abrasive wheel, stone, belt, paste, sheet, compound, slurry, etc. Takes various forms: surface grinding (creates flat and/or squared surfaces); cylindrical grinding (for external cylindrical and tapered shapes, fillets, undercuts, etc.); centerless grinding; chamfering; thread and form grinding; tool and cutter grinding; offhand grinding; lapping and polishing (grinding with extremely fine grits to create ultrasmooth surfaces); honing; and disc grinding.
- modular design ( modular construction)
modular design ( modular construction)
Manufacturing of a product in subassemblies that permits fast and simple replacement of defective assemblies and tailoring of the product for different purposes. See interchangeable parts.
- turning
turning
Workpiece is held in a chuck, mounted on a face plate or secured between centers and rotated while a cutting tool, normally a single-point tool, is fed into it along its periphery or across its end or face. Takes the form of straight turning (cutting along the periphery of the workpiece); taper turning (creating a taper); step turning (turning different-size diameters on the same work); chamfering (beveling an edge or shoulder); facing (cutting on an end); turning threads (usually external but can be internal); roughing (high-volume metal removal); and finishing (final light cuts). Performed on lathes, turning centers, chucking machines, automatic screw machines and similar machines.