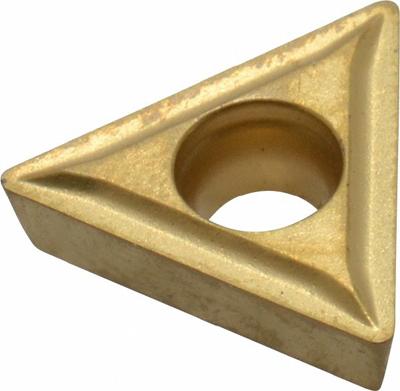
MSC Industrial Supply Co. is significantly expanding its Hertel line of metalworking products. This expanded offering features a wide range of new tools, including material-specific turning insert grades, spotting drills, combined drill and countersink tools as well as additional solid carbide roughing end mills. In addition to these enhancements, a threading solution has been added to the company's proprietary cutoff and grooving system to help drive greater efficiencies.
"We are constantly looking for opportunities to bring new solutions to market that will not only meet our customers' needs, but help them optimize their businesses," said Brian McGrath, MSC's Senior Product Manager for Hertel. "We recognized the need for more enhanced lines of Hertel tooling in response to our customers evolving needs. Hertel is synonymous with performance, increased productivity, cost control and profitability, and it was our goal to give them more selection to achieve their business goals."
Hertel has historically offered a full line of general turning inserts in common geometries, sizes and multiple grades. Its portfolio includes high-speed steel, cobalt and carbide drills in a variety of lengths, such as jobber, screw machine and taper. Threading products are available in general purpose hand, spiral point and spiral fluted taps with taper, plug or bottoming chamfers. Hertel offers a full line of general purpose end mills, including roughing, ball nose, square end, 2-flute, 3-flute, multi-flute and double-ended products.
The range of expanded tooling now also includes:
• Hertel turning insert products, including HC115T turning grade for steel, HP410T/HT410T grades for nonferrous materials, and HP510T grade for high temperature alloys. The new grades are available in a comprehensive selection of insert shapes and chip control geometries for fine finishing, medium, and roughing applications. In addition we've also added our next generation of insert grades which include HC1250T, HP225T, HC405T and HC315T. These new grades and chip breaker geometries work across a wide variety of applications, including steel, stainless steels and cast iron.
• HertelNotch is the new comprehensive grooving and threading platform which includes inserts, tool holders and spare parts, all designed to cover a wide range of materials.
• A threading solution adds to MSC's cut-off and grooving system, increasing its flexibility and effectiveness. The system incorporates various combinations of inserts, blades and monoblock tool holders that enable tooling to be exactly tailored to specific production needs. Customers can select from material-specific grades to drive the most productivity in various work piece materials.
• More than 250 new Hertel spotting drills and combined drill and countersink tools join the hole-making tool line. With 60ÌÜÅÁ, 90ÌÜÅÁ and 120ÌÜÅÁ point geometries, the HSS and cobalt tools can meet a wide range of application requirements.
• Added versions of workhorse M42 cobalt roughing end mills include new sizes, coatings and fine and coarse roughing geometries.
Contact Details
Related Glossary Terms
- alloys
alloys
Substances having metallic properties and being composed of two or more chemical elements of which at least one is a metal.
- countersink
countersink
Tool that cuts a sloped depression at the top of a hole to permit a screw head or other object to rest flush with the surface of the workpiece.
- cutoff
cutoff
Step that prepares a slug, blank or other workpiece for machining or other processing by separating it from the original stock. Performed on lathes, chucking machines, automatic screw machines and other turning machines. Also performed on milling machines, machining centers with slitting saws and sawing machines with cold (circular) saws, hacksaws, bandsaws or abrasive cutoff saws. See saw, sawing machine; turning.
- grooving
grooving
Machining grooves and shallow channels. Example: grooving ball-bearing raceways. Typically performed by tools that are capable of light cuts at high feed rates. Imparts high-quality finish.
- high-speed steels ( HSS)
high-speed steels ( HSS)
Available in two major types: tungsten high-speed steels (designated by letter T having tungsten as the principal alloying element) and molybdenum high-speed steels (designated by letter M having molybdenum as the principal alloying element). The type T high-speed steels containing cobalt have higher wear resistance and greater red (hot) hardness, withstanding cutting temperature up to 1,100º F (590º C). The type T steels are used to fabricate metalcutting tools (milling cutters, drills, reamers and taps), woodworking tools, various types of punches and dies, ball and roller bearings. The type M steels are used for cutting tools and various types of dies.
- metalworking
metalworking
Any manufacturing process in which metal is processed or machined such that the workpiece is given a new shape. Broadly defined, the term includes processes such as design and layout, heat-treating, material handling and inspection.
- stainless steels
stainless steels
Stainless steels possess high strength, heat resistance, excellent workability and erosion resistance. Four general classes have been developed to cover a range of mechanical and physical properties for particular applications. The four classes are: the austenitic types of the chromium-nickel-manganese 200 series and the chromium-nickel 300 series; the martensitic types of the chromium, hardenable 400 series; the chromium, nonhardenable 400-series ferritic types; and the precipitation-hardening type of chromium-nickel alloys with additional elements that are hardenable by solution treating and aging.
- threading
threading
Process of both external (e.g., thread milling) and internal (e.g., tapping, thread milling) cutting, turning and rolling of threads into particular material. Standardized specifications are available to determine the desired results of the threading process. Numerous thread-series designations are written for specific applications. Threading often is performed on a lathe. Specifications such as thread height are critical in determining the strength of the threads. The material used is taken into consideration in determining the expected results of any particular application for that threaded piece. In external threading, a calculated depth is required as well as a particular angle to the cut. To perform internal threading, the exact diameter to bore the hole is critical before threading. The threads are distinguished from one another by the amount of tolerance and/or allowance that is specified. See turning.
- turning
turning
Workpiece is held in a chuck, mounted on a face plate or secured between centers and rotated while a cutting tool, normally a single-point tool, is fed into it along its periphery or across its end or face. Takes the form of straight turning (cutting along the periphery of the workpiece); taper turning (creating a taper); step turning (turning different-size diameters on the same work); chamfering (beveling an edge or shoulder); facing (cutting on an end); turning threads (usually external but can be internal); roughing (high-volume metal removal); and finishing (final light cuts). Performed on lathes, turning centers, chucking machines, automatic screw machines and similar machines.