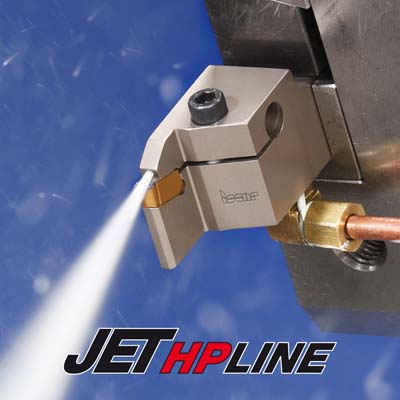
A complete line of standard tools for High Pressure Coolant (HPC) turning from Iscar Metals Inc. puts more efficient turning of titanium, Inconel, and stainless steel within easy reach of any shop. Previously, HPC tooling was available only as a special. Manufacturers can now get the same quick delivery and security of supply for HPC tools as for any standard tool.
In combination with optional standard high pressure plumbing readily available on virtually all mainstream turning machines, ISCAR JETHP (Jet High Pressure) tools bring three key benefits on these problematic metals. They consistently end chip jamming, improve tool life more than 10 to 1, while doubling removal rates. HPC turning has been proven effective for decades as a stable, safe process, especially on titanium. The obstacle has been that it required custom coolant plumbing and special tools. More recently, most machine builders have made high pressure coolant plumbing capability a standard option. Now ISCAR has completed the HPC chain by standardizing the tooling as well and making it as easy to use as regular tooling.
The ISCAR JETHP family covers the full range of turning, grooving and parting tools and includes HPC versions of the company's ISOTURN, HELITURN, TANG-GRIP, PENTACUT and CUT- GRIP tools, in both standard and interchangeable-tool CAMFIX styles. Their design derives from more than a decade of ISCAR experience in supplying special HPC tooling to hundreds of manufacturers, mostly titanium fabricators. All styles feature internal coolant paths compatible with through-spindle plumbing in the machine.
The JETHP line also includes all connection accessories as standard. HPC turning works by aiming a high pressure "hydraulic wedge" of liquid coolant precisely into the cutting zone, shattering chips into uniformly small, classic C-shapes and ejecting them completely out of the way. In addition, because it remains liquid at such high pressures and flow rates, it lubricates and cools the cutting area more effectively. Between 40 and 400 bars pressure, the higher the pressure, the smaller the chip in titanium, Inconel and long-chipping stainless steels.
In the ISCAR ISOTURN line, two separate streams simultaneously deliver coolant to the top rake and bottom flank of the tool. The nozzle for the top stream can be aimed and uniquely, is easy to move out of the way for convenient insert indexing and replacement. It automatically snaps back into place when coolant is turned back on. The bottom stream can be turned on to enhance the cooling effect. Other models in the line have discharge points, always targeting the cutting zone. With all the uncertainty taken out of the HPC turning process, practitioners can avoid all the unavoidable bottlenecks associated with turning titanium, Inconel and stainless steel.
Contact Details
Related Glossary Terms
- coolant
coolant
Fluid that reduces temperature buildup at the tool/workpiece interface during machining. Normally takes the form of a liquid such as soluble or chemical mixtures (semisynthetic, synthetic) but can be pressurized air or other gas. Because of water’s ability to absorb great quantities of heat, it is widely used as a coolant and vehicle for various cutting compounds, with the water-to-compound ratio varying with the machining task. See cutting fluid; semisynthetic cutting fluid; soluble-oil cutting fluid; synthetic cutting fluid.
- grooving
grooving
Machining grooves and shallow channels. Example: grooving ball-bearing raceways. Typically performed by tools that are capable of light cuts at high feed rates. Imparts high-quality finish.
- parting
parting
When used in lathe or screw-machine operations, this process separates a completed part from chuck-held or collet-fed stock by means of a very narrow, flat-end cutting, or parting, tool.
- rake
rake
Angle of inclination between the face of the cutting tool and the workpiece. If the face of the tool lies in a plane through the axis of the workpiece, the tool is said to have a neutral, or zero, rake. If the inclination of the tool face makes the cutting edge more acute than when the rake angle is zero, the rake is positive. If the inclination of the tool face makes the cutting edge less acute or more blunt than when the rake angle is zero, the rake is negative.
- stainless steels
stainless steels
Stainless steels possess high strength, heat resistance, excellent workability and erosion resistance. Four general classes have been developed to cover a range of mechanical and physical properties for particular applications. The four classes are: the austenitic types of the chromium-nickel-manganese 200 series and the chromium-nickel 300 series; the martensitic types of the chromium, hardenable 400 series; the chromium, nonhardenable 400-series ferritic types; and the precipitation-hardening type of chromium-nickel alloys with additional elements that are hardenable by solution treating and aging.
- turning
turning
Workpiece is held in a chuck, mounted on a face plate or secured between centers and rotated while a cutting tool, normally a single-point tool, is fed into it along its periphery or across its end or face. Takes the form of straight turning (cutting along the periphery of the workpiece); taper turning (creating a taper); step turning (turning different-size diameters on the same work); chamfering (beveling an edge or shoulder); facing (cutting on an end); turning threads (usually external but can be internal); roughing (high-volume metal removal); and finishing (final light cuts). Performed on lathes, turning centers, chucking machines, automatic screw machines and similar machines.