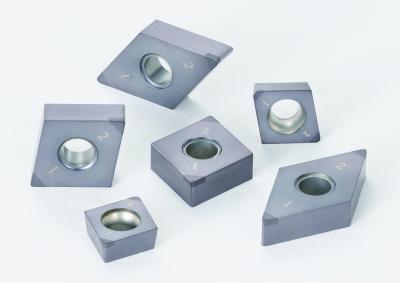
When turning steel above 45 Rc, it is advantageous to choose a CBN insert grade that can stand up to multiple hard turning operations and produce the finish, stability, and tool life needed to power through a variety of parts. Turning parts that have sections of continuous surfaces mixed with interruptions like automotive suspension, shafts, or gears requires repeatable tooling options that perform well in different situations. To give manufacturers a larger range of hard turning capabilities, Kyocera is introducing the brand new KBN020 high-performing CBN grade.
Kyocera’s KBN020 excels as a 1st choice, general purpose CBN grade with a broad application range from continuous to heavily interrupted machining. Utilizing innovative new layering techniques, Kyocera has developed the MEGACOAT TOUGH coating technology. This coating combines a highly wear-resistant layer on the surface adhered to high-content CBN which is used to toughen up the edge for greater fracture resistance when encountering interruptions. The adhesion layer is laminated between the wear-resistance layer and the CBN to reduce layer peeling for longer tool life and stable machining. Providing both excellent wear resistance and fracture resistance gives the user more flexibility, range, performance, and tool life when turning hardened materials.
To take full advantage of Kyocera’s new hard turning technology, it is important to follow the listed speed and feed recommendations to make the most out of your tool life and surface finish.
Benefits:
- Combining new coating technology with high-content CBN provides exceptional wear and fracture resistance
- KBN020 supports a wide range of hardened applications from continuous to heavily interrupted machining
- Extended lineup of cutting edge preparations for various applications
- Excellent surface finish
Features:
- Full lineup of negative and positive insert geometries
- Variety of edge preps available
- MEGACOAT TOUGH coating technology for extended tool life
- Multiple cutting edges per insert
- Improved adhesion between CBN and high wear resistance layer
Applications:
- Recommended for hardened materials (55 HRc or more)
- External and internal turning, facing, boring
Contact Details
Related Glossary Terms
- boring
boring
Enlarging a hole that already has been drilled or cored. Generally, it is an operation of truing the previously drilled hole with a single-point, lathe-type tool. Boring is essentially internal turning, in that usually a single-point cutting tool forms the internal shape. Some tools are available with two cutting edges to balance cutting forces.
- cubic boron nitride ( CBN)
cubic boron nitride ( CBN)
Crystal manufactured from boron nitride under high pressure and temperature. Used to cut hard-to-machine ferrous and nickel-base materials up to 70 HRC. Second hardest material after diamond. See superabrasive tools.
- feed
feed
Rate of change of position of the tool as a whole, relative to the workpiece while cutting.
- hard turning
hard turning
Single-point cutting of a workpiece that has a hardness value higher than 45 HRC.
- turning
turning
Workpiece is held in a chuck, mounted on a face plate or secured between centers and rotated while a cutting tool, normally a single-point tool, is fed into it along its periphery or across its end or face. Takes the form of straight turning (cutting along the periphery of the workpiece); taper turning (creating a taper); step turning (turning different-size diameters on the same work); chamfering (beveling an edge or shoulder); facing (cutting on an end); turning threads (usually external but can be internal); roughing (high-volume metal removal); and finishing (final light cuts). Performed on lathes, turning centers, chucking machines, automatic screw machines and similar machines.
- wear resistance
wear resistance
Ability of the tool to withstand stresses that cause it to wear during cutting; an attribute linked to alloy composition, base material, thermal conditions, type of tooling and operation and other variables.