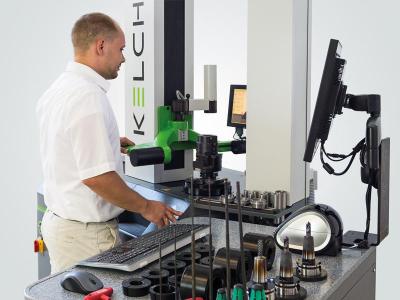
Kelch offers a new system concept for a tool presetter from the KELCH KENOVA set line V9xx-S range. The focus here is on the redesign of the shrink fit equipment and side unit. The redesign also incorporates a redesigned control panel and innovative components, including an operating monitor with touchscreen with an ergonomically designed holder for optimum operating convenience. “Once again Kelch is setting new benchmarks in the design of tool presetters. Handling is made significantly easier, thanks to the new shrink fit cooling concept. The benefits for users include the convenient operation of the unit coupled with maximum precision. After all, Kelch has over 75 years of experience in this field,” explains Viktor Grauer (B. Eng), member of the executive board and head of innovation management at Kelch.
A combined tool presetter and shrink fit device for the precise and repeatable presetting of tools in shrink fit holders to a target dimension represents the pinnacle of tool presetting. Kelch has rigorously redesigned its KaliTec system, which has proved itself over many years and resulted in the KENOVA set line V9-S system.
Kelch has fully redesigned the tower design for all Premium Line series units (V6, V9 und V9-S) . The basic design of the tower is made of highly rigid grey cast iron and the design has been systematically simplified. Additional component options, including cutting edge monitor, turning centre and grinding camera, can be very easily attached to the new tower. A laser pointer (laser class 1) integrated in the camera holder is also new and is used for improved visual locating of the cutting edge.
New fixed shrink fit equipment has been designed for the V9 basic machine. The position of the tower on the V9 basic body has been chosen to enable convenient and accessible handling. The shrink fit equipment is fixed on the right front side of the V9 basic body using a stable bracket adapter, which enables tools with a max. Ø of 420 mm to be measured.
A smoke extraction unit is also optionally available for the shrink fit equipment. The stop ring can be swapped easily and quickly, as with the previous unit. EASY operating software has been adapted for ease of access: in the event of a service, the software moves the coil body into a conveniently accessible replacement position.
Kelch has fully redesigned the side unit: all the key components for the “shrink fitting” and “cooling” workflows are accommodated in the side unit. The induction coil control and cooling unit are integrated in the lower part of the side unit. The close positioning of the side unit to the V9 presetter helps to ensure that there are no long distances between the work processes shrinkingwith measurement and cooling. There is space on the worktop of the side unit for a label printer alongside the adapters, cooling bushings, cooling stations etc. needed for shrinking.
A data printer can be held on the side of the side unit with a separate holder. Users also have the opportunity to attach additional brackets at the side, which provide space for storing additional spindle inserts and tool holders in the KELCH Tul system.
The side unit is equipped, as standard, with a wireless keyboard and wireless mouse, which further simplifies operation of the unit.
The innovative control panel stands out on account of the fact that the motorised adjustment of the X, Z and C axes is done using a joystick instead of using cursor keys. The X and Z linear axes are controlled by steering the joystick in the direction indicated by the arrows on the cover panel. A push-button is incorporated in the top of the joystick to move the C axis. All 3 axes can be moved simultaneously. A toggle button incorporated in the top of the joystick switches between fast mode and creep speed for each movement of the axis.
A further unique feature is the fixture of an optionally available operating monitor with touch function. While the standard monitor is fixed on the side unit on the side facing the user, the touch version is supplied with a swivel arm for ease of operation and can be positioned by the user according to their body position.
Contact Details
Related Glossary Terms
- fixture
fixture
Device, often made in-house, that holds a specific workpiece. See jig; modular fixturing.
- grinding
grinding
Machining operation in which material is removed from the workpiece by a powered abrasive wheel, stone, belt, paste, sheet, compound, slurry, etc. Takes various forms: surface grinding (creates flat and/or squared surfaces); cylindrical grinding (for external cylindrical and tapered shapes, fillets, undercuts, etc.); centerless grinding; chamfering; thread and form grinding; tool and cutter grinding; offhand grinding; lapping and polishing (grinding with extremely fine grits to create ultrasmooth surfaces); honing; and disc grinding.
- turning
turning
Workpiece is held in a chuck, mounted on a face plate or secured between centers and rotated while a cutting tool, normally a single-point tool, is fed into it along its periphery or across its end or face. Takes the form of straight turning (cutting along the periphery of the workpiece); taper turning (creating a taper); step turning (turning different-size diameters on the same work); chamfering (beveling an edge or shoulder); facing (cutting on an end); turning threads (usually external but can be internal); roughing (high-volume metal removal); and finishing (final light cuts). Performed on lathes, turning centers, chucking machines, automatic screw machines and similar machines.