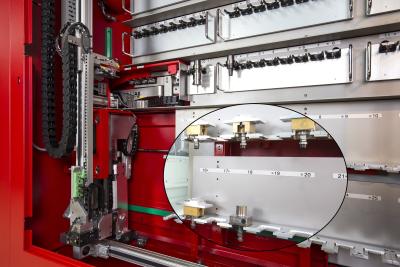
KERN Precision says the new KERN MicroPro 4/5-axis milling machine is designed with production and productivity in mind. It is powered by the highly productive HSK40 spindle with feed ranges up to 1,181 ipm and 42,000 rpm.
Smart solutions made it possible to bring maximum performance down to a footprint of less than 45 sq. ft. KERN has stepped up the engineering challenge by combining a workpiece changer and toolchanger into the tool cabinet in the machine. It offers the end user the choice of utilizing all 209 toolholders or a combination of 102 toolholders and an Integrated workpiece changer that's able to hold 30 Erowa or 3R pallets.
These 30 pallets in the internal workpiece changer enable unmanned lights out production for several hours or possibly overnight to ensure a quick return on investment. Also, it is possible to extend the capacity with an additional external workpiece changer. Another "space saver" is the unified Heidenhain TNC640 control that aligns directly with the machine.
All of this is supported by the the company's Ultra High Performance (UHP) UniCore machine platform that is thermosymmetrically designed. Engineered with enhanced damping behavior and the capability to absorb vibrations, the UHP UniCore platform reportedly enables maximum machine stability. Taken even one step further, the UniCore platform optimizes flow through with the elimination of interfaces making it easier to clean and maintain.
KERN’s focus on serial production of complex and high precision parts can be seen throughout the engineering and components incorporated into the KERN MicroPro. The HSK40 spindle provides high precision and high chip removal rates to boost production and impart high-quality surface finishes. Fully integrated 4th and 5th axes provide a dynamic system for true 5-axis machining.
Contact Details
Related Glossary Terms
- feed
feed
Rate of change of position of the tool as a whole, relative to the workpiece while cutting.
- gang cutting ( milling)
gang cutting ( milling)
Machining with several cutters mounted on a single arbor, generally for simultaneous cutting.
- inches per minute ( ipm)
inches per minute ( ipm)
Value that refers to how far the workpiece or cutter advances linearly in 1 minute, defined as: ipm = ipt 5 number of effective teeth 5 rpm. Also known as the table feed or machine feed.
- milling
milling
Machining operation in which metal or other material is removed by applying power to a rotating cutter. In vertical milling, the cutting tool is mounted vertically on the spindle. In horizontal milling, the cutting tool is mounted horizontally, either directly on the spindle or on an arbor. Horizontal milling is further broken down into conventional milling, where the cutter rotates opposite the direction of feed, or “up” into the workpiece; and climb milling, where the cutter rotates in the direction of feed, or “down” into the workpiece. Milling operations include plane or surface milling, endmilling, facemilling, angle milling, form milling and profiling.
- milling machine ( mill)
milling machine ( mill)
Runs endmills and arbor-mounted milling cutters. Features include a head with a spindle that drives the cutters; a column, knee and table that provide motion in the three Cartesian axes; and a base that supports the components and houses the cutting-fluid pump and reservoir. The work is mounted on the table and fed into the rotating cutter or endmill to accomplish the milling steps; vertical milling machines also feed endmills into the work by means of a spindle-mounted quill. Models range from small manual machines to big bed-type and duplex mills. All take one of three basic forms: vertical, horizontal or convertible horizontal/vertical. Vertical machines may be knee-type (the table is mounted on a knee that can be elevated) or bed-type (the table is securely supported and only moves horizontally). In general, horizontal machines are bigger and more powerful, while vertical machines are lighter but more versatile and easier to set up and operate.
- toolchanger
toolchanger
Carriage or drum attached to a machining center that holds tools until needed; when a tool is needed, the toolchanger inserts the tool into the machine spindle. See automatic toolchanger.