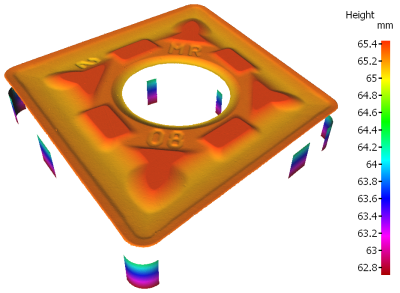
So far, geometries such as the bore holes of injection valves in the automotive industry, for example, could hardly be measured optically. Lateral probing of components with vertical surfaces was limited to tactile measuring systems, CT solutions or complex special solutions. This changes with a new function of the optical coordinate measuring system µCMM from Bruker Alicona. Vertical surfaces of more than 90° can now also be measured optically.
µCMM is a purely optical coordinate measuring machine that enables the measurement of dimension, position, shape and roughness of smallest tolerances contact-free and with only one sensor. Now, a new feature of this coordinate measuring system also allows the lateral probing of components. Component features such as holes, bores, reference surfaces, contours and lengths can thus be optically measured with high accuracy, high resolution and in short measurement times.
The diameter-depth ratio of holes ranges from 1:3 to 1:10, the measurable diameter is 0.1 mm to 2 mm. Users measure parameters such as outside and inside diameter and opening angle. In combination with an automatic rotation unit "µCMM Real3D," turning the 3-axis CMM into a 5-axis system, multiple holes including their orientation to each other can be measured. One application which can be achieved using the µCMM in combination with Real3D is the measurement of injection nozzles including diameter, K-factor, injection angle and side angle.
The patent pending method for hole measurement "Vertical Focus Probing" is an extension of the Focus-Variation technology and is based on the use of a partial light cone. Individual light rays diffusely reflected from vertical surfaces are captured by the lens. Flanks with more than 90° are traceably measured in high resolution and high repeatability. Vertical flanks measured in this way can be used, for example, to fit a workpiece coordinate system.
µCMM allows highly accurate measurement of smallest tolerances, even on large components. 3D data is captured areal based and in high measurement point density, which, in addition to measuring dimensional parameters, also enables the measurement of roughness according to EN ISO 4287/88 (Ra, Rq, Rz ...) and 25178 (Sa, Sq, Sz ...). Due to the high accuracy of the axes, individual measurements are precisely related to each other. Users can also verify the position of their components in this way. Therefore, it is no longer necessary to measure the entire component optically as it is sufficient to measure only those areas that are relevant. For a user, this means a significant reduction in overall measuring time.
Contact Details
Related Glossary Terms
- turning
turning
Workpiece is held in a chuck, mounted on a face plate or secured between centers and rotated while a cutting tool, normally a single-point tool, is fed into it along its periphery or across its end or face. Takes the form of straight turning (cutting along the periphery of the workpiece); taper turning (creating a taper); step turning (turning different-size diameters on the same work); chamfering (beveling an edge or shoulder); facing (cutting on an end); turning threads (usually external but can be internal); roughing (high-volume metal removal); and finishing (final light cuts). Performed on lathes, turning centers, chucking machines, automatic screw machines and similar machines.