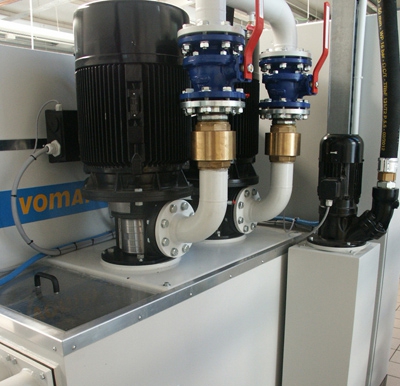
The right filtration system in a tool grinding operation is an important part of the value chain and a prerequisite for high quality and uninterrupted production. Fine filtration systems developed by Vomat Inc., distributed by oelheld U.S. Inc., grow thanks to the availability of a variety of add-on modules to individually configure and tailor systems. The cleaner a grinding lubricant can be kept and the less often it needs to be replaced, the more savings a tool grinder can realize. The cost for tools, filters and lubricants will decrease. In addition, machine downtime is minimized.
Jan Froehlich, production manager at VOMAT, states: "The choice of the right filtration and cooling has an immediate impact on the manufacturing costs of the end product. Vomat filter systems ensure a 100 percent separation of dirty and clean oil. On-demand filtering and filter back-washing provide coolants to NAS 7 (3-5µm) quality combined with significantly increased service life of the lubricant."
The FA-series platform of standard equipment allows VOMAT to design a system that meets customer specifications and individual requirements and which best fits into the workflow of the tool grinder. These can be single units with 120 liters per minute fluid throughput up to central filtration systems which supply complete machine shops. Through a multitude of additional components and options such as cooling modules, machine supply pumps, auxiliary tanks, remote servicing, and disposal concepts, the systems can be adapted and optimized to customer-specific system requirements.
Froehlich remarks: "With some before-hand planning, Vomat's ZFH-1200 series can be adapted to changing production requirements or capacities. This results in maximum efficiency in various stages of production and business development. Vomat systems are always optimally adapted to the individual needs of the user."
Contact Details
Related Glossary Terms
- grinding
grinding
Machining operation in which material is removed from the workpiece by a powered abrasive wheel, stone, belt, paste, sheet, compound, slurry, etc. Takes various forms: surface grinding (creates flat and/or squared surfaces); cylindrical grinding (for external cylindrical and tapered shapes, fillets, undercuts, etc.); centerless grinding; chamfering; thread and form grinding; tool and cutter grinding; offhand grinding; lapping and polishing (grinding with extremely fine grits to create ultrasmooth surfaces); honing; and disc grinding.