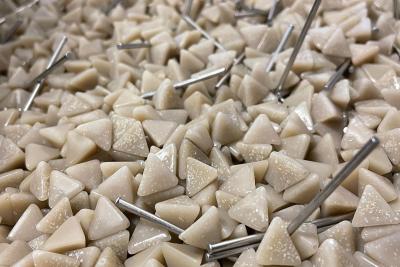
When it comes to achieving the required quality of products by surface refinement, the mass finishing technology can be used for a broad range of different finishing tasks. With its comprehensive research & development activities the Rösler Oberflächentechnik GmbH continues to generate new technical highlights not only for the machine technology but also for the respective mass finishing consumables. Three recently introduced products make it possible to significantly improve the finishing results, the process consistency, the cost efficiency and sustainability of mass finishing operations. At the same time, they open the door for new applications, for example, the finishing of complex, cup-shaped work pieces.
The mass finishing technology can handle all kinds of surface finishing tasks ranging from the simple deburring/edge radiusing and surface grinding to high gloss polishing of mass- produced bulk goods and single components. It can even create special effects on the surface of the work pieces. Of course, like any other industrial processes, mass finishing operations must comply with all kinds of requirements such as high quality standards, process stability, work piece traceability and cost-efficiency. More recently optimal resource utilization and sustainability have become a focal point in numerous industries. And finally, the rapidly growing automatization and digitization of manufacturing operations also calls for specially adapted solutions for mass finishing operations. For decades the Rösler Oberflächentechnik GmbH has met these challenges with comprehensive research and development in the equipment sector as well as in the fields of process and automation technology and consumables. In this context a big advantage is that Rösler is producing all its consumables in-house. Rüdiger Böhm, global R&D manager at Rösler, explains: "We study the technical trends and requirements in numerous industries and markets extensively. Our findings are then systematically utilized for the development of innovative products to provide a significant incremental value to our customers and to expand the application range for the mass finishing technology.”
MultiShape – a unique media shape that makes the impossible possible
Such an innovation is the new MultiShape ceramic media. Compared to all other products currently available in the market, this media has a patented shape without any flat, parallel surface areas. On the one hand this unique design prevents media lodging in the work pieces, which can occur particularly in case of complex work pieces. Such lodged media can severely affect the finishing process and must frequently be removed by hand. On the other hand, the shape with its rounded surface areas allows the surface refinement of work pieces, which to-date could not be handled by mass finishing at all or only with very complicated operational setups. This includes components with difficult-to-reach surface areas like tight radii, undercuts, notches and slits, which can frequently be found in stamped and bent components. The unusual ceramic media also allows the effective and homogeneous finishing of external and internal surface areas on tube segments and cup-shaped components like housings and deep drawn parts.
Compared to traditional ceramic media, the new product is also characterized by a faster and more dynamic motion of the work piece/media mix and a higher material removal rate. This results in up to 10% shorter finishing times. Therefore, the new media represents a significant contribution towards higher productivity and cost-efficiency. Another important attribute of the MultiShape media are its uniform wear characteristics. This excellent shape retention feature allows a longer media use, which is positively affecting the operating costs. The grinding intensity can be adjusted to the respective finishing application through different ceramic compositions.
Mass finishing without foaming – increased process stability, efficiency and sustainability
Unwanted foam is a common phenomenon in mass finishing processes with plastic media, even with foam-reduced media versions. Foaming can be problematic because, acting as a buffer between the work pieces and media, it reduces the grinding performance and material removal rate. This can diminish the process stability, and the processing aim can frequently no longer be achieved within the defined cycle time. Moreover, the foam containing metal and media fines contaminates the surface of the finished work pieces. The foam also causes a deterioration of the process water cleanliness, requiring a higher compound dosing rate and forcing the user to replace the process water more frequently. Last-but-not-least, foam discharged from the mass finishing machine contaminates the working environment. In the past the users tried to control the foaming by adding special chemical compounds. But this was not very successful, caused additional costs and reduced the process sustainability.
With its non-foaming plastic media, the so-called “N” version, the R&D department at Rösler has now developed a better solution. Christian Höhn, head of the technology management at Rösler, explains: ”Prior to introducing the product in the market we conducted extensive field trials with special pilot users. The trials proved convincingly that the non-foaming plastic media has the same grinding characteristics and performance as the standard product”. The trials also demonstrated that with the newly developed media the mass finishing processes are running much more stable, and the required results are achieved in shorter cycle times. This positive effect regarding cost-efficiency and sustainability is augmented by a longer usable life of the media and process water and a reduced compound usage. ”Because of the disruptive foaming many users had been using ceramic media, even though this was not the best option. For these users the non- foaming plastic media version is a great opportunity to optimize their finishing processes”, concludes Christian Höhn. All plastic media in the comprehensive Rösler portfolio are available in the non-foaming “N” version.
Dust-free drying with organic drying media
The third new development in the consumables sector in 2021 allows a significant reduction of the dust occurring during drying processes utilizing organic drying media such as maizorb. Even in small quantities the liquid, easily dispensable, Anti-Dust additive significantly reduces the formation of dust. Depending on the operating times and work pieces the additive can be manually added or dosed fully automatically.
The Anti-Dust additive is employed in drying operations for metal and plastic components, whenever organic drying media is used. Without negatively impacting the drying performance it guarantees absolutely spot-free surface finishes. At the same time, dust residues on the finished work pieces and the surrounding area are minimized. This also represents a huge step towards a clean, low-dust working environment. Rainer Schindhelm, division manager of the consumables production, explains: „Because it is purely organic and complies with the prevailing food standards, the Anti-Dust additive also represents a significant contribution towards a cleaner environment.”
Contact Details
Related Glossary Terms
- flat ( screw flat)
flat ( screw flat)
Flat surface machined into the shank of a cutting tool for enhanced holding of the tool.
- grinding
grinding
Machining operation in which material is removed from the workpiece by a powered abrasive wheel, stone, belt, paste, sheet, compound, slurry, etc. Takes various forms: surface grinding (creates flat and/or squared surfaces); cylindrical grinding (for external cylindrical and tapered shapes, fillets, undercuts, etc.); centerless grinding; chamfering; thread and form grinding; tool and cutter grinding; offhand grinding; lapping and polishing (grinding with extremely fine grits to create ultrasmooth surfaces); honing; and disc grinding.
- parallel
parallel
Strip or block of precision-ground stock used to elevate a workpiece, while keeping it parallel to the worktable, to prevent cutter/table contact.
- polishing
polishing
Abrasive process that improves surface finish and blends contours. Abrasive particles attached to a flexible backing abrade the workpiece.
- surface grinding
surface grinding
Machining of a flat, angled or contoured surface by passing a workpiece beneath a grinding wheel in a plane parallel to the grinding wheel spindle. See grinding.