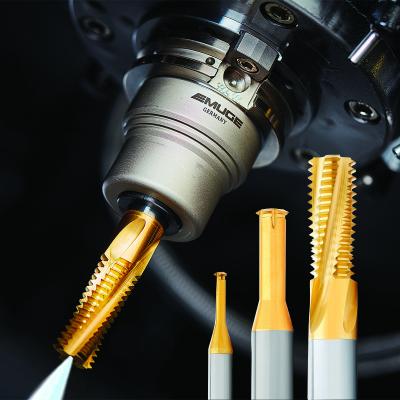
EMUGE-FRANKEN USA, a leading manufacturer of high-performance taps, thread mills, end mills, drills, and other rotary tools, has announced the launch of a new line of multipurpose thread mills designed for threading a wide range of standard materials efficiently and economically. Ideal for job shop manufacturing where part applications and materials frequently change, EMUGE MultiTHREAD™ Thread Mills provide a versatile solution for many threadmaking requirements.
MultiTHREAD Thread Mills enable shops to boost their production output and save on threadmaking costs, as fewer types of thread mills need to be stocked in the tool crib and the possibility of broken taps and scrapped parts are eliminated. “MultiTHREAD cuts most materials that job shops encounter while providing thread accuracy, quality and finish with high process security and control,” said Marlon Blandon, EMUGE-FRANKEN USA Thread Milling Product Manager.
MultiTHREAD Thread Mills feature a proprietary TIN T21 coating developed by EMUGE, which reduces chip welding and improves chip evacuation. MultiTHREAD Thread Mills also allow one tool to thread both through and blind holes and make right or left-hand threads. Two types of sub-micro grain carbide thread mills are offered – full form or single plane. Full form thread mills that machine threads in one timesaving cutting rotation, feature a rigid core diameter that reduces deflection. The single plane design enables one tool to produce multiple thread sizes and allows the pitch diameter to be controlled.
EMUGE MultiTHREAD Thread Mills are available in a broad range of types and sizes. Full form 2XD thread mills range from No.10 to 3/4ʺ sizes in solid tools, and 1/4ʺ to 1ʺ sizes in coolant-through tools. Full form thread mills are also available in metric sizes. Single plane 2XD thread mills range from No. 0 to 3/4ʺ including STI sizes in inch, and 3XD single plane mills range from No. 2 to 3/4ʺ. Single plane models are available in either solid, or coolant-through on larger sizes. In total, over 80 SKUs of MultiTHREAD tools are stocked as standard.
Contact Details
Related Glossary Terms
- gang cutting ( milling)
gang cutting ( milling)
Machining with several cutters mounted on a single arbor, generally for simultaneous cutting.
- milling
milling
Machining operation in which metal or other material is removed by applying power to a rotating cutter. In vertical milling, the cutting tool is mounted vertically on the spindle. In horizontal milling, the cutting tool is mounted horizontally, either directly on the spindle or on an arbor. Horizontal milling is further broken down into conventional milling, where the cutter rotates opposite the direction of feed, or “up” into the workpiece; and climb milling, where the cutter rotates in the direction of feed, or “down” into the workpiece. Milling operations include plane or surface milling, endmilling, facemilling, angle milling, form milling and profiling.
- pitch
pitch
1. On a saw blade, the number of teeth per inch. 2. In threading, the number of threads per inch.
- threading
threading
Process of both external (e.g., thread milling) and internal (e.g., tapping, thread milling) cutting, turning and rolling of threads into particular material. Standardized specifications are available to determine the desired results of the threading process. Numerous thread-series designations are written for specific applications. Threading often is performed on a lathe. Specifications such as thread height are critical in determining the strength of the threads. The material used is taken into consideration in determining the expected results of any particular application for that threaded piece. In external threading, a calculated depth is required as well as a particular angle to the cut. To perform internal threading, the exact diameter to bore the hole is critical before threading. The threads are distinguished from one another by the amount of tolerance and/or allowance that is specified. See turning.
- titanium nitride ( TiN)
titanium nitride ( TiN)
Added to titanium-carbide tooling to permit machining of hard metals at high speeds. Also used as a tool coating. See coated tools.