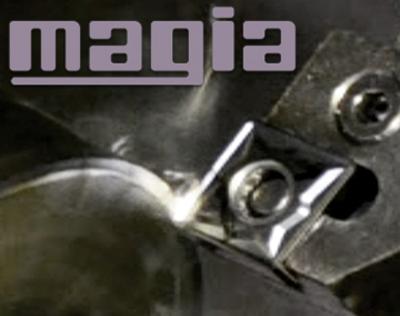
In its on-going effort to offer cutting tools designed to simplify manufacturing processes, Nexus Cutting Tools unveiled the newest addition to its line of high-performance turning inserts, Magia LT1000.
According to Nexus, Magia inserts provide unmatched hardness and toughness, excellent for cutting stainless and hardened alloys. Magia inserts feature a specially formulated PVD TiAIN coating that is almost 4X thicker than industry standard PVD inserts. Mark Frost, National Sales Representative for Nexus, says, "Thicker and more consistent PVD means our inserts last longer and wear more evenly. Our customers average a 250 percent improvement in tool life compared to their other PVD inserts."
According to Frost, Magia inserts increase depth-of-cut and feed rates compared to standard inserts, while providing excellent surface finish throughout the life of the insert.
Contact Details
Related Glossary Terms
- alloys
alloys
Substances having metallic properties and being composed of two or more chemical elements of which at least one is a metal.
- feed
feed
Rate of change of position of the tool as a whole, relative to the workpiece while cutting.
- hardness
hardness
Hardness is a measure of the resistance of a material to surface indentation or abrasion. There is no absolute scale for hardness. In order to express hardness quantitatively, each type of test has its own scale, which defines hardness. Indentation hardness obtained through static methods is measured by Brinell, Rockwell, Vickers and Knoop tests. Hardness without indentation is measured by a dynamic method, known as the Scleroscope test.
- physical vapor deposition ( PVD)
physical vapor deposition ( PVD)
Tool-coating process performed at low temperature (500° C), compared to chemical vapor deposition (1,000° C). Employs electric field to generate necessary heat for depositing coating on a tool’s surface. See CVD, chemical vapor deposition.
- turning
turning
Workpiece is held in a chuck, mounted on a face plate or secured between centers and rotated while a cutting tool, normally a single-point tool, is fed into it along its periphery or across its end or face. Takes the form of straight turning (cutting along the periphery of the workpiece); taper turning (creating a taper); step turning (turning different-size diameters on the same work); chamfering (beveling an edge or shoulder); facing (cutting on an end); turning threads (usually external but can be internal); roughing (high-volume metal removal); and finishing (final light cuts). Performed on lathes, turning centers, chucking machines, automatic screw machines and similar machines.