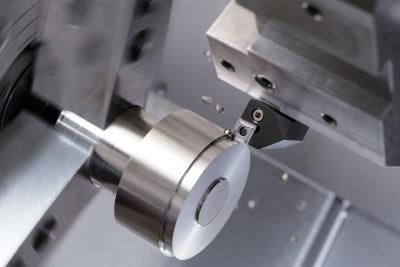
Machining heat-resistant alloys and stainless steel can present numerous challenges, including rapid insert degradation, deterioration of dimensional accuracy, poor chip control, burrs, increased cutting forces, and excessive heat generation. Kyocera is excited to unveil the PR115S/PR120S series, a comprehensive solution designed to tackle these challenges head-on. With outstanding heat resistance, wear resistance, and stability, this series ensures prolonged tool life and enables stable machining of heat-resistant alloys.
The PR115S/PR120S series features Kyocera’s new MEGACOAT TOUGH HRSA proprietary coating technology, offering exceptional endurance and maximum tool life for machining heat-resistant super alloys (HRSA). The inserts consist of four distinct layers. The first layer utilizes thick-film PVD coating technology, suppressing abrasive wear, and reducing notch damage with its ultra-fine grain structure. The second layer, a TiAlN coating, provides superior oxidation resistance and controls crater wear. The third layer serves as an adhesion layer between the carbide substrate and the main coating layers, enhancing adhesion and scratch resistance. The fourth layer is a unique carbide substrate, formulated specifically for heat-resistant alloy machining, with excellent thermal properties and high thermal conductivity. The PR115S employs a mixed structure of fine and coarse grain carbide for improved heat and wear resistance, while the PR120S utilizes a coarser grain structure for heat resistance and more stability.
When combined with these new coatings, Kyocera’s optimized chipbreaker designs for heat-resistant alloy (SQ/SG/SX) enhance machining stability. The SQ chipbreaker is ideal for finishing to medium machining applications, offering extended tool life, reduced temperature at the cutting edge, and decreased burring.
The SG chipbreaker is optimized for roughing, providing a well-balanced rake face shape for extended tool life and a shallow bottom chipbreaker design for smooth chip control during heavy machining. The SX chipbreaker excels in high-efficiency roughing, featuring a rake design that reduces the temperature at the cutting edge and a unique cutting-edge design with a 60° lead angle.
Benefits:
-
MEGACOAT TOUGH HRSA coating offers exceptional endurance and maximum tool life for machining heat-resistant super alloys (HRSA)
-
Multi-layer structure provides exceptional resistance to wear, notch damage, coating scratching, crater wear, and oxidation
Features:
-
Large lineup of inserts from finishing to roughing
-
Three different HRSA-optimized chipbreakers available SQ, SG, and SX
-
Positive rake inserts available for machining small parts
-
Options for continuous, light-interrupted, interrupted, and heavy-
interrupted machining
-
Multiple cutting edges per insert
Applications:
-
Heat-resistant alloys such as Inconel® 718
-
Stainless Steel
-
External and internal turning, facing, boring
Contact Details
Related Glossary Terms
- abrasive
abrasive
Substance used for grinding, honing, lapping, superfinishing and polishing. Examples include garnet, emery, corundum, silicon carbide, cubic boron nitride and diamond in various grit sizes.
- alloys
alloys
Substances having metallic properties and being composed of two or more chemical elements of which at least one is a metal.
- boring
boring
Enlarging a hole that already has been drilled or cored. Generally, it is an operation of truing the previously drilled hole with a single-point, lathe-type tool. Boring is essentially internal turning, in that usually a single-point cutting tool forms the internal shape. Some tools are available with two cutting edges to balance cutting forces.
- chipbreaker
chipbreaker
Groove or other tool geometry that breaks chips into small fragments as they come off the workpiece. Designed to prevent chips from becoming so long that they are difficult to control, catch in turning parts and cause safety problems.
- lead angle
lead angle
Angle between the side-cutting edge and the projected side of the tool shank or holder, which leads the cutting tool into the workpiece.
- physical vapor deposition ( PVD)
physical vapor deposition ( PVD)
Tool-coating process performed at low temperature (500° C), compared to chemical vapor deposition (1,000° C). Employs electric field to generate necessary heat for depositing coating on a tool’s surface. See CVD, chemical vapor deposition.
- rake
rake
Angle of inclination between the face of the cutting tool and the workpiece. If the face of the tool lies in a plane through the axis of the workpiece, the tool is said to have a neutral, or zero, rake. If the inclination of the tool face makes the cutting edge more acute than when the rake angle is zero, the rake is positive. If the inclination of the tool face makes the cutting edge less acute or more blunt than when the rake angle is zero, the rake is negative.
- titanium aluminum nitride ( TiAlN)
titanium aluminum nitride ( TiAlN)
Often used as a tool coating. AlTiN indicates the aluminum content is greater than the titanium. See coated tools.
- turning
turning
Workpiece is held in a chuck, mounted on a face plate or secured between centers and rotated while a cutting tool, normally a single-point tool, is fed into it along its periphery or across its end or face. Takes the form of straight turning (cutting along the periphery of the workpiece); taper turning (creating a taper); step turning (turning different-size diameters on the same work); chamfering (beveling an edge or shoulder); facing (cutting on an end); turning threads (usually external but can be internal); roughing (high-volume metal removal); and finishing (final light cuts). Performed on lathes, turning centers, chucking machines, automatic screw machines and similar machines.
- wear resistance
wear resistance
Ability of the tool to withstand stresses that cause it to wear during cutting; an attribute linked to alloy composition, base material, thermal conditions, type of tooling and operation and other variables.