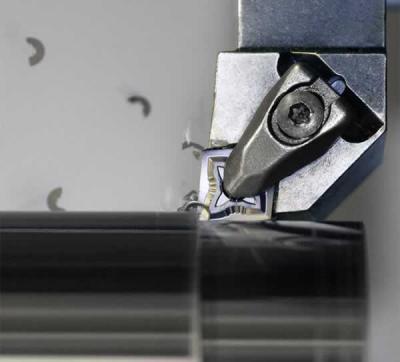
Dormer Pramet, Elgin, Ill., now offers Pramet SF and SM geometries for machining of high temperature alloys and stainless steel, the company announced Jan. 27.
The two geometries are new to the Dormer Pramet indexable offering.
- The SF geometry features a sharp positive geometry with an inclination cutting edge of 14.5° and is said to be suitable for finishing applications in continuous cut with very low cutting forces.
- The SM chip-breaker is reportedly a wear-resistant, universal geometry for medium machining (finishing up to roughing), and suitable for continuous and interrupted cut.
According to Dormer Pramet, both new chip-breakers are suitable for materials with poor machinability, such as stainless steels, mild steels and high-temperature alloys. The new geometries are available in a variety of grades and have been designed to promote low cutting forces and prevent work-hardening, which reportedly reduces the risk of vibration when turning thin-walled components.
The new geometries also are suitable for use with two new turning grades now available. The PVD coated Pramet T6310 grade features enhanced cutting edge reliability and strength with intermediate Cobalt content substrate for additional hardness and increased abrasion resistance, which is said to enable prolonged tool life. Pramet T6310's triple coating provides durability for higher cutting speeds when machining stainless steel, heat-treated and hardened materials, according to the company.
Contact Details
Related Glossary Terms
- alloys
alloys
Substances having metallic properties and being composed of two or more chemical elements of which at least one is a metal.
- hardness
hardness
Hardness is a measure of the resistance of a material to surface indentation or abrasion. There is no absolute scale for hardness. In order to express hardness quantitatively, each type of test has its own scale, which defines hardness. Indentation hardness obtained through static methods is measured by Brinell, Rockwell, Vickers and Knoop tests. Hardness without indentation is measured by a dynamic method, known as the Scleroscope test.
- interrupted cut
interrupted cut
Cutting tool repeatedly enters and exits the work. Subjects tool to shock loading, making tool toughness, impact strength and flexibility vital. Closely associated with milling operations. See shock loading.
- machinability
machinability
The relative ease of machining metals and alloys.
- physical vapor deposition ( PVD)
physical vapor deposition ( PVD)
Tool-coating process performed at low temperature (500° C), compared to chemical vapor deposition (1,000° C). Employs electric field to generate necessary heat for depositing coating on a tool’s surface. See CVD, chemical vapor deposition.
- stainless steels
stainless steels
Stainless steels possess high strength, heat resistance, excellent workability and erosion resistance. Four general classes have been developed to cover a range of mechanical and physical properties for particular applications. The four classes are: the austenitic types of the chromium-nickel-manganese 200 series and the chromium-nickel 300 series; the martensitic types of the chromium, hardenable 400 series; the chromium, nonhardenable 400-series ferritic types; and the precipitation-hardening type of chromium-nickel alloys with additional elements that are hardenable by solution treating and aging.
- turning
turning
Workpiece is held in a chuck, mounted on a face plate or secured between centers and rotated while a cutting tool, normally a single-point tool, is fed into it along its periphery or across its end or face. Takes the form of straight turning (cutting along the periphery of the workpiece); taper turning (creating a taper); step turning (turning different-size diameters on the same work); chamfering (beveling an edge or shoulder); facing (cutting on an end); turning threads (usually external but can be internal); roughing (high-volume metal removal); and finishing (final light cuts). Performed on lathes, turning centers, chucking machines, automatic screw machines and similar machines.